Labeling machine parts encompass a range of sophisticated components designed to handle different aspects of the labeling process. From the feeding and cutting of labels to the precise application of products, each part contributes to the overall performance and reliability of the machine.
Assistance and service are crucial in maintaining and operating labeling machines effectively. Expert guidance and maintenance support ensure that the machines run efficiently, enhancing customer satisfaction and operational reliability.
Manufacturers and operators rely on these parts to achieve high labeling accuracy and efficiency, meeting diverse labeling requirements across industries such as pharmaceuticals, food and beverage, cosmetics, and more.
Main components
We will introduce labeler components in six sections:
Feeding system
Generally speaking, feeding systems are divided into two types: horizontal and turntable, but they share common properties.
- Main feeding wheel: Responsible for pulling labels from the roll and feeding them into the labeling process.
- Auxiliary feeding wheel: Supports the main feeding wheel by ensuring continuous and stable label supply.
- Feeding motor: Powers the feeding wheels and controls the speed of label delivery, crucial for synchronization with product movement.
Having reliable labeler parts is essential for maintaining the functionality and efficiency of the feeding system.
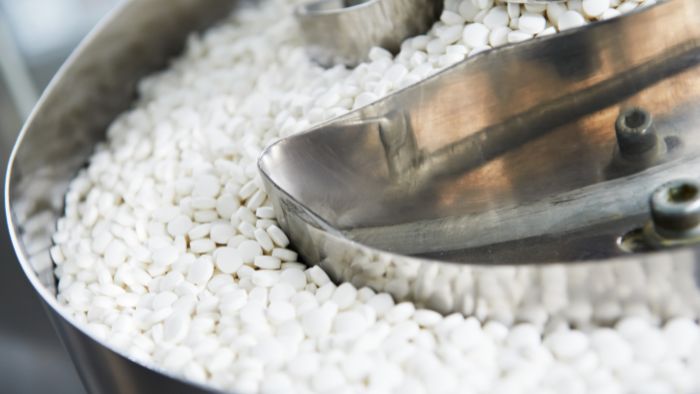
Label cutting system
- Cutting blade assembly: Cut labels to the required length before application.
- Cutting motor: Drives the cutting blade assembly, synchronized with label feeding to ensure precise cutting at high speeds.
We also offer a wide range of certified and genuine replacement parts for the cutting system to minimize downtime and maximize productivity.
Label sensing system
- Sensors: Includes optical sensors and pressure sensors to detect labels, and gaps between labels, and ensure proper alignment and application to maximize efficiency and accuracy.
- Sensor types and functions: Optical sensors detect label presence and position, while pressure sensors ensure labels adhere uniformly and accurately.
Control system
- PLC controller: Manages the overall operation of the labeling machine, coordinating actions between different parts for seamless performance.
- HMI interface: Provides a user-friendly interface for operators to monitor machine status, adjust settings, and troubleshoot issues efficiently.
- Control panel and buttons: Enables manual control and adjustment of parameters such as label length, speed, and alignment during setup and operation.
Having spare parts for the control system is crucial to ensure continuous operation and minimize downtime.
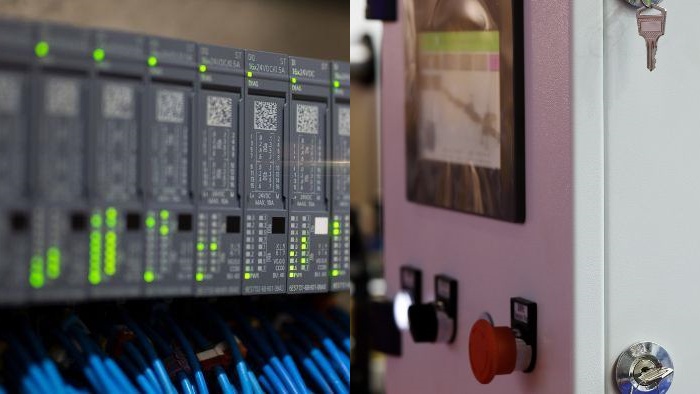
Electrical system
- Main electrical cabinet: Houses electrical components, including relays, circuit breakers, and power supplies, ensuring safe and reliable electrical operation.
- Cables and wiring: Connects various electrical components and ensures proper power distribution throughout the machine.
Mechanical structure
- Mainframe: Provides structural support and stability for all moving parts and components.
- Drive systems: Includes chains, belts, and gears that transmit motion from motors to feeding and cutting mechanisms.
- Adjustment and fastening devices: Allows for precise alignment and secure attachment of components, crucial for maintaining operational accuracy over time.
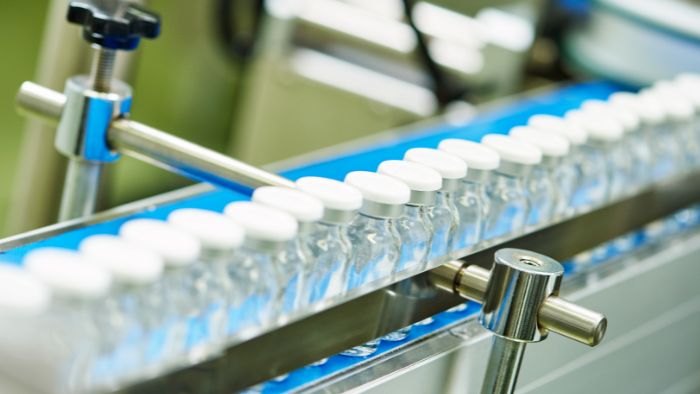
Viallabeller‘s pharmaceutical labeling machines are equipped with all of the above accessories and can be customized to meet your needs. Not only that, but we also offer a wide range of solutions for labeling pharmaceutical containers, such as ampoules, syringes, tamper-evident, auto-injectors, vials, bottles, tubes, and cartons.
Key functions and requirements
Labeling machine parts must meet stringent criteria for accuracy, speed, versatility, and reliability:
- Labeling accuracy and speed: Parts must work together to achieve precise label placement within specified tolerances at high speeds, minimizing waste and optimizing production output.
- Compatibility with label sizes and materials: Parts should accommodate various label dimensions and materials, including paper, plastic, and specialty labels used in different industries.
- Safety and Reliability: Components must adhere to safety standards, ensuring operator protection and minimizing downtime due to malfunctions or maintenance.
Market trends and technological developments
The labeling machine industry is evolving with advancements in automation, connectivity, and environmental sustainability:
- Automation advancements: Increasing integration of robotics and AI for autonomous operation and adaptive labeling processes.
- Smart and connected machines: IoT-enabled machines that provide real-time data monitoring, predictive maintenance, and remote troubleshooting capabilities.
- Environmental considerations: Energy-efficient designs and materials that reduce carbon footprint and support sustainable manufacturing practices.
Conclusion
In conclusion, understanding the intricacies of labeling machine parts is essential for maximizing operational efficiency and product quality in industrial labeling applications. Each component—from feeding systems to control mechanisms—plays a critical role in ensuring accurate and reliable label application.
As technology advances, labeling machine parts continues to evolve, incorporating innovations that enhance performance, reduce costs, and meet the dynamic demands of modern manufacturing environments. Embracing these advancements ensures that labeling machine parts remains at the forefront of efficient and sustainable labeling solutions across industries.