Label rolls are important tools used in many industries. They help with labeling and identifying products. In logistics, retail, and manufacturing, label rolls make it easy to organize and track items. They also improve product packaging.
This guide looks at label rolls in detail. It covers what they are made of, how they are used, how they are made, and current market trends.
By learning about these topics, businesses can use label rolls to work more efficiently and meet modern needs.
Components of custom-printed roll labels
A label roll has a simple structure, but each part is important. The main parts are the label material, the adhesive backing, and the printing method. Each component helps the label work well.
Choosing the right label design is also important. Different materials work better for specific uses. For example, BOPP labels resist moisture, while textured paper looks nice and appealing.
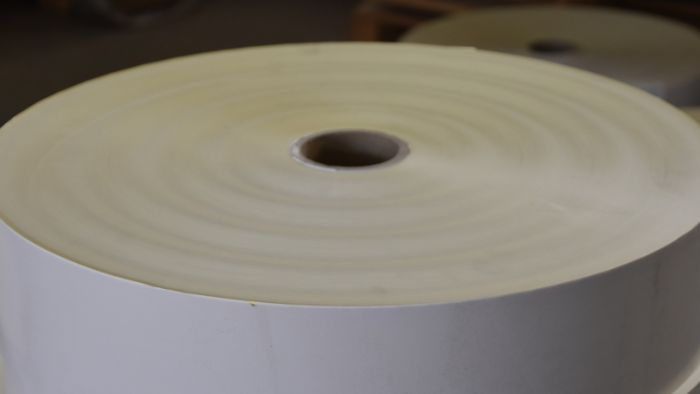
High-quality materials
Label rolls come in different materials based on their use. Common options are paper, plastic, and synthetic films. White vinyl is strong and shiny, making it good for both indoor and outdoor use.
Paper labels are popular because they are affordable and easy to print. White laid texture is often used for wine bottle labels and handwritten mailing labels. It has a nice, subtle texture.
For places that need strong labels, plastic or synthetic films are better. These materials resist moisture and chemicals, making them last longer in tough conditions.
Adhesive
The adhesive on the back of label rolls is very critical. The type of adhesive depends on the surface and conditions where the label will be used.
Permanent adhesives work well for labels that need to stay put for a long time. Removable adhesives let you take off labels easily without leaving sticky residue.
Some adhesives are made for special situations, like freezer-grade adhesives for cold storage.
Label printing technology
The information on label rolls is printed using different technologies. Common methods include thermal transfer, direct thermal, and laser printing.
Thermal transfer printing uses a ribbon to transfer ink onto the label material. This method creates durable labels that resist fading. In contrast, direct thermal printing does not use ink. Instead, it relies on heat-sensitive paper that darkens when heated.
Direct thermal printing is best for short-term use because the print can fade over time. Laser printing provides high-resolution images and is great for labels needing detailed graphics or barcodes.
Label printing is essential for businesses. It improves product packaging and organization. This process also offers cost savings, efficient application, and many customization options to fit various business needs.
Applications of label roll
Label rolls are used in many industries for different purposes. Custom roll labels are flexible and improve product packaging and branding. They are also helpful for organization and shipping tasks.
Logistics
In logistics, label rolls are essential for tracking shipments and managing inventory. Labels show important details like tracking numbers, addresses, and barcodes.
These can be scanned easily throughout the supply chain. Using label rolls helps improve efficiency and reduces errors, making operations smoother.
Retail
The retail industry relies on label rolls for pricing and product information. Labels are on almost every item in a store. They provide details like price, ingredients, and the manufacturer. Custom-printed roll labels help reduce waste and allow for faster printing.
They are easy to use with machines or by hand. Promotional labels highlight discounts and special offers, influencing what customers buy. Retailers use custom labels to strengthen their brand identity, making label rolls important for marketing.
Product Labels in Manufacturing
In manufacturing, label rolls are important for product identification and quality control. Labels help ensure products are easy to identify and meet regulations. They can include information like the product’s origin, batch number, expiration date, and safety instructions. This information helps with traceability and compliance.
Labels are also used during assembly to mark parts and components. This helps make production efficient and reduces mistakes.
Pharmaceutical Applications
Pharmaceutical labeling machines use high-quality self-adhesive label rolls for various containers. These include ampoules, vials, syringes, and tamper-evident packaging. This ensures that pharmaceutical companies maintain high labeling standards.
Production process of label roll
The production of label rolls includes several important steps. Each step helps make sure the final product is high quality.
Design and layout
Before making label rolls, the design and layout are planned carefully. This includes choosing the right material, adhesive, and printing method for the specific use.
During the design phase, the text, barcodes, and images are arranged on the label. This helps make sure everything is easy to read and follows rules. Customers can use an online design tool to create custom labels. They can upload logos, add text, and choose colors easily.
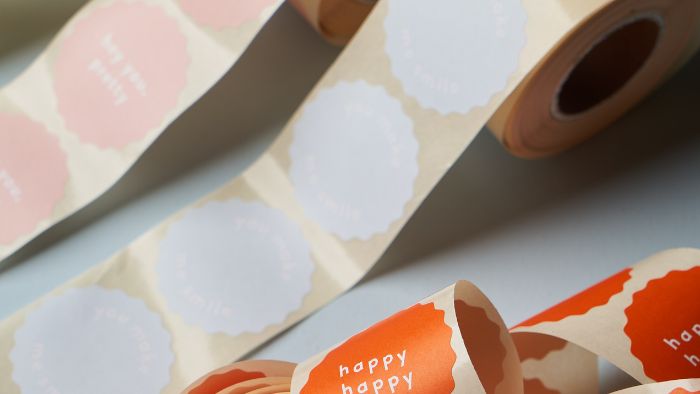
Manufacturing process
After the design is approved, the process to make label rolls starts. First, the right label material is chosen and prepared. This material goes into a printing press. Depending on the printing method, the labels are printed with the needed information.
Once printed, the labels are cut to size, either one by one or in a continuous roll. The last step is to add the adhesive backing and roll the labels onto a core, creating the finished label roll.
Quality control
Quality control is very important in the production process. Each batch of label rolls is tested carefully. This ensures that the labels stick well, the print quality is good, and the labels can handle their intended conditions.
Tests may check for adhesive strength, print durability, and resistance to things like moisture and temperature.
Market trends in label roll
The label roll market is changing due to new technology and consumer needs. Several factors affect the cost of custom roll labels. These factors include size, material, and quantity.
Customers can use tools like product calculators to estimate costs based on their needs. Additionally, bulk printing can help save money.
Technological innovations
New materials and printing technology are making label rolls stronger and more flexible. Innovations like RFID labels allow for wireless tracking and data storage. These labels are becoming popular in logistics and retail.
Also, eco-friendly materials are being created to meet the demand for sustainable products. Label dispensers improve efficiency in applying labels. They make it easier to manage and apply roll labels quickly, saving time and reducing manual work.
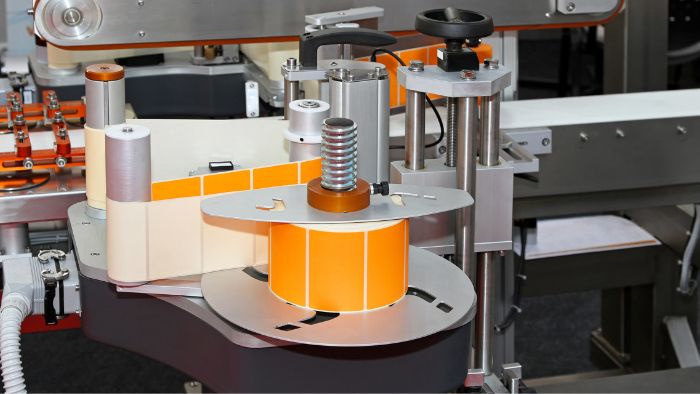
Environmental concerns
Sustainability is a big trend in the label roll industry. Many companies want to lower their impact on the environment. This has led to labels made from recycled materials and safer adhesives.
The focus on sustainability will keep growing, affecting how products are made and what materials are used.
Market demand
The need for label rolls is expected to increase in many industries. This growth comes from the rise of e-commerce, stricter regulations, and the need for better supply chain management.
As businesses aim to improve operations and traceability, label rolls will play a more important role.
Choosing the right label size is key for different uses, like mailing labels, product branding, and wine bottle labels. Common sizes are designed for each specific application.
Conclusion
In conclusion, label rolls are a crucial tool across a range of industries, offering solutions for everything from product labeling to compliance with regulations.
As technology advances and sustainability becomes more of a focus, the label roll industry will continue to innovate, meeting the evolving needs of businesses worldwide. Whether in logistics, retail, or manufacturing, the use of label rolls will remain integral to efficient operations and effective product management.