How does drug get to the shelves? It’s important to know the steps involved.
First, scientists work in a lab to create the drug. They test it to make sure it is safe. After that, the drug is made in a factory.
The drug then goes through careful checks to make sure it is high quality. Finally, it is sent to stores where people can buy it. This article explains each step of this process.
Drug receipt and inspection
Supplier shipment
Drugs start their journey when they are shipped from the supplier. They are carefully packed and have papers to track them.
Transport monitoring
While the drugs are being moved, special checks keep an eye on temperature and humidity. This helps keep the drugs safe.
Arrival inspection and counting
When the drugs arrive, they are checked carefully. The number of items is counted to make sure the right amount was delivered. They also check if any drugs are damaged.
Damage confirmation
If any drugs are damaged, they are marked and reported. Only the good, undamaged drugs move to the next step.
Drug information entry
Basic information entry
Write down important details about each drug. This includes the name, dosage, and who made it.
Batch numbers and production dates
Record the batch numbers and when the drug was made. This helps track the drug’s journey. The information is attached to the packaging by a drug labeling machine, like a medicine box labeling machine. It’s important to check this information carefully.
Expiration date verification
Check the expiration dates to make sure the drugs are still good before they are sold.
System entry and label printing
After checking all details, enter the information into the computer system. Then, print labels for the drugs to use later.
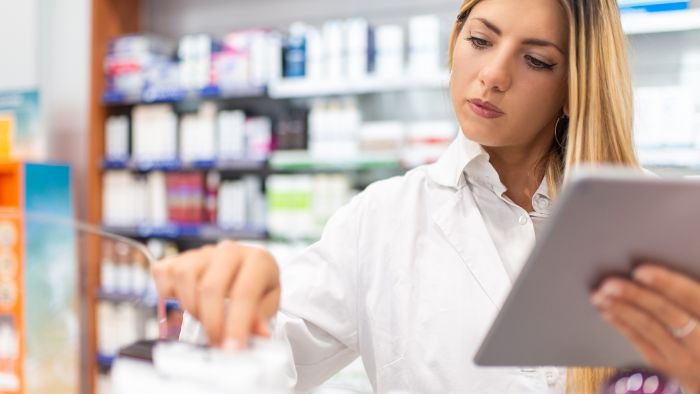
Drug quality inspection in the drug development process
Visual inspection
Look carefully at the drugs to find any physical problems or mistakes.
Quality testing
Test samples from each batch to check their quality. Use data from clinical trials to make sure the drugs work well.
Standards compliance check
Compare the drugs to set rules to make sure they meet all safety and quality standards.
Quality report generation
After testing, create a report. This report shows the results and confirms that the drugs are safe to sell.
Drug storage
Categorized placement
Drugs are sorted by type and storage requirements. This makes it easy to manage inventory and find drugs quickly.
Temperature and humidity control
Storage conditions are checked to keep drugs safe. Some drugs need special storage, like refrigerators.
Special storage conditions
Drugs that need special care, like controlled substances or biologics, are stored in the right conditions.
Inventory system updates
The inventory management system is updated to show current stock levels and where drugs are stored.
Drug display on pharmacy shelves
Shelf placement planning
Drugs are placed on shelves in a way that helps people find them easily.
Confirmation of display location
Each drug’s spot on the shelf is checked to make sure it matches the plan.
Shelf label setting
Shelves get labels with drug names, dosages, and prices to help people choose.
Completion confirmation
A final check makes sure all drugs are in the right place and labels are correct.
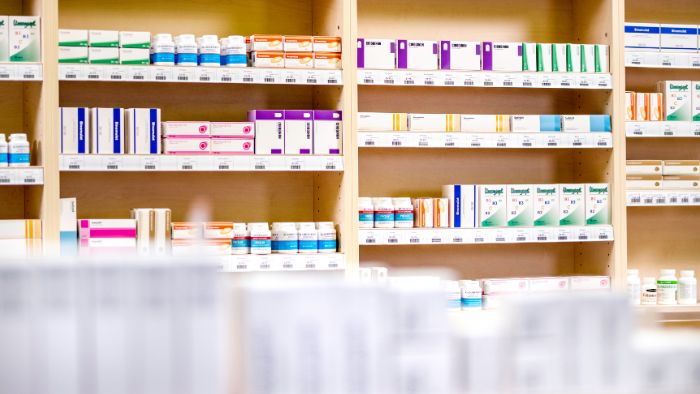
System updates and maintenance
Inventory quantity updates
The amount of medicine is checked and updated to keep records right.
System status checks
The inventory system is checked often to make sure it works.
Data backup
Copies of inventory data are made to keep it safe.
Anomaly handling
Problems in the inventory are fixed right away.
Daily management and monitoring
Inventory audits
Regular checks are done to make sure records match the stock.
Expiration date monitoring
The system gives alerts when medicines are close to expiring.
Stock replenishment and adjustment
Medicine levels are checked, and new orders are made to keep enough stock.
Safety checks and records
Storage areas are checked to keep drugs safe, and reports are written down.
Issue handling by a regulatory authority
Damaged drug management
Damaged drugs are found, taken out of stock, and thrown away safely.
Expired drug removal
Expired drugs are taken off the shelves and disposed of properly.
Customer feedback handling
Customer feedback is collected to find and fix problems with drug quality.
Implementation of improvement measures
Changes are made based on feedback to make drug handling better.
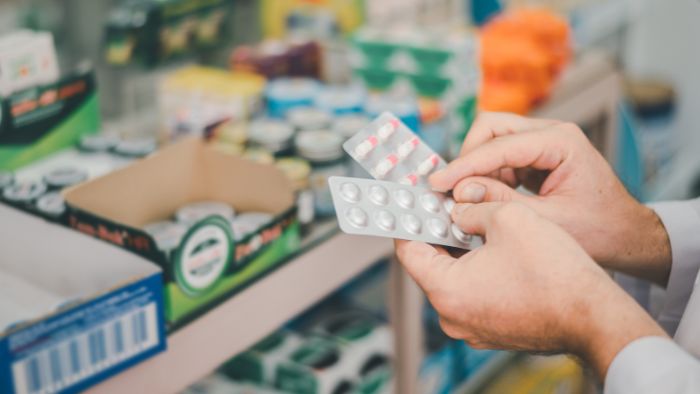
Conclusion
The process of how does drug get to the shelves is long and careful. It has many steps to make sure the drugs are safe and ready for people to use.
Each step, from getting the drug to putting it on the shelf, helps keep the drug safe and good to use. Record-keeping, quality checks, and inventory control are all part of this process.
Before a drug is sold, it must be approved. This approval shows the drug is safe. This careful process follows the rules and helps people trust the medicine they buy.