In various industries, cylindrical products such as bottles, cans, and jars are a common choice for packaging due to their practical shape and efficient use of space. This article explores the essentials of labeling such containers, which is crucial for brand recognition, regulatory compliance, and consumer information.
The process of labeling cylindrical containers varies significantly across different sectors due to distinct requirements concerning durability, aesthetics, and material resistance.
Types of cylindrical containers and labeling requirements by industry
Each industry has specific needs that dictate the type of cylindrical containers used and the labeling requirements.
- Food and beverage industry: This sector often uses glass and plastic bottles. Labels need to withstand moisture and varying temperatures, especially when products are refrigerated or frozen. Hence, waterproof and low-temperature-resistant labels are common. Clear and readable labels are crucial for consumer information and effective branding in the food industry. Additionally, labeling machines specifically designed for wine bottles and other cylindrical containers ensure compliance with legal requirements and enhance the visual appeal of the products.
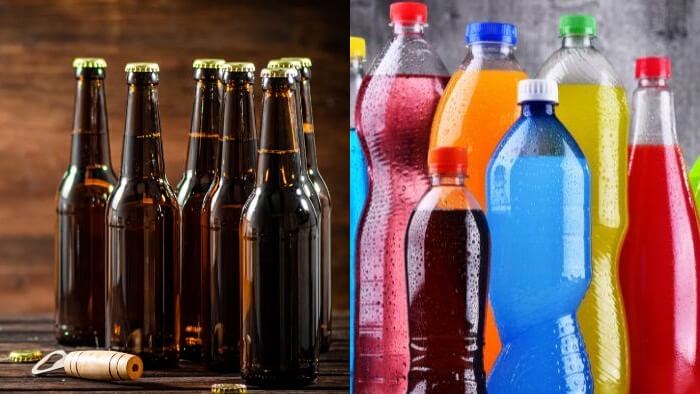
- Cosmetics industry: Containers such as spray bottles and lotion containers made from plastics or glass require labels that not only provide product information but also contribute to the aesthetic appeal. The labels must resist chemicals found in cosmetics to remain intact and legible. Labeling machines designed for round containers are highly efficient and speedy, catering to high-volume labeling needs.
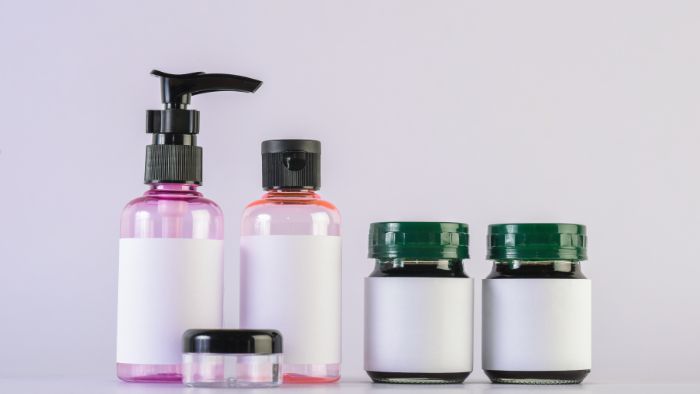
- Pharmaceutical industry: Precision in labeling is paramount. Containers typically include glass vials, small cylindrical containers that can’t stand upright, and plastic bottles that store medicines and reagents. Labels must provide exact details about contents and usage instructions and are often made with materials resistant to chemicals and environmental conditions. On the other hand, the right pharmaceutical labeling machine is equally important.
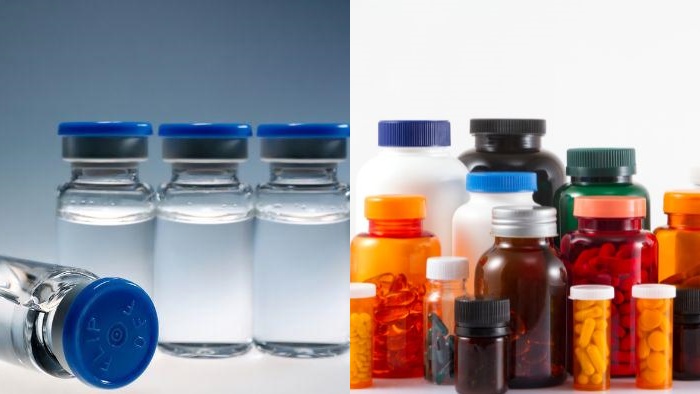
- Chemical industry: Containers like chemical storage bottles used for storing chemicals demand highly durable labels that can withstand exposure to harsh substances and extreme temperatures. These labels must include detailed handling and hazard information, adhering to strict regulatory standards

Label placement and methods
The placement and method of label application play a significant role in the functionality and visibility of the information.
Label placement
- Body labeling: Most common for displaying brand and product information.
- Neck labeling: Used for tamper-evidence or first-opening indication.
- Base labeling: Ideal for information like production dates and batch numbers, which are important for tracking but secondary to the consumer.
Know more: Different Medicine Labeling Positions
Labeling methods
- Single-sided labeling: Suitable for containers that will be displayed in a uniform manner, providing essential information on the front.
- Double-sided labeling: Best for products requiring more extensive information, such as ingredients and usage instructions, visible from both sides.
- Wrap-around labeling: Offers maximum area coverage and is excellent for products that benefit from high visual impact and information accessibility. Wrap-around labeling For the pharmaceutical industry, some bottles, such as ampoules and medicine bottles, can maximize the display of information, and our wrap-around labeling solution can meet this requirement.
- Horizontal labeling: Ideal for cylindrical containers such as vials, bottles, or tubes, ensuring accurate and consistent label placement around the circumference. This method is particularly effective for products that require full 360-degree labeling, providing ample space for branding, instructions, and regulatory information. Our horizontal labeling solutions meet these requirements. Semi-automatic labeling machines are designed to apply adhesive labels to cylindrical containers, showcasing their efficiency and adaptability for various product types and sizes. Electric bottle label applicators equipped with a foot pedal enhance ease of operation and efficiency by allowing operators to use both hands for labeling while controlling the machine’s functionality with their foot.
Labeling machinery and technology
Choosing the right machinery and technology for labeling is crucial to meet the specific needs of cylindrical container labeling:
Machinery options: Automated and semi-automated labeling machines are available, with choices largely dictated by the scale of operations and the precision required. Manual labeling machines are user-friendly and require minimal training, making them suitable for businesses with smaller production runs. Semi-automatic labeling machines are the perfect solution for both small-scale productions and larger operations.
Technological considerations: Key factors include the speed of application, label adhesion quality, and the ability to handle various label materials and container sizes. It is important to consider production speed when purchasing a bottle labeling machine. Label applicator machines can automatically label up to 80 round products per minute.
Conclusion
Labeling cylindrical containers effectively requires a comprehensive understanding of industry-specific requirements, appropriate label placement, and the selection of suitable labeling methods and machinery.
By focusing on these aspects, businesses can ensure their products are attractively presented and comply with relevant regulations, enhancing overall brand integrity.