Turntable feeding systems are pivotal in modern manufacturing and packaging lines, offering precise, efficient, and reliable means of handling materials. These systems facilitate the movement and positioning of products through a rotating platform, ensuring consistent workflow and minimizing human error. Turntable feeding systems are connected to various components like counting machines and air jet cleaners, ensuring continuous operation and a smooth flow of containers while preventing jams and maintaining a streamlined process.
This guide explores the intricacies of turntable feeding systems, highlighting their operation, types, applications, and benefits.
Overview of turntable feeding systems
Turntable feeding systems consist of a rotating platform powered by motors that can be adjusted for speed and direction. The diameter of the products is crucial in determining their compatibility with the turntable feeding system. Products are placed on the turntable, which rotates to align them with packaging or assembly lines.
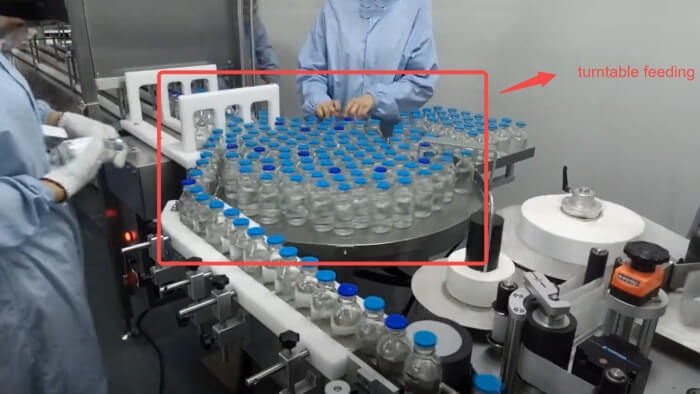
Common in industries where precision and repeatability are crucial, these systems are designed to handle various products ranging from small electronic components to large containers.
Working principle
The core mechanism of a turntable feeder involves a motor-driven platform that rotates at predetermined intervals. Sensors and programmable logic controllers (PLCs) typically govern the system, ensuring feed bottles are efficiently transported to the next stage of processing, such as filling and labeling, to maintain the flow of operations without interruption.
Types of turntable feeding systems to feed bottles
- Manual turntables: Operated by hand, suitable for low-volume or bespoke operations.
- Motorized turntables: Electric motors are used to automate the feeding process, which is ideal for high-volume production lines.
- Programmable turntables: Allow for adjustment of speed and rotation patterns, catering to complex industrial applications.
- Used in handling glass bottles in automated production systems.
Applications in various industries
Turntable feeding systems are versatile and can be found in:
- Pharmaceuticals: Handling and organizing bottles or vials for filling, labeling, and capping.
- Food and beverage: Positioning containers for labeling, filling, or capping in a sanitary environment. Turntable feeding systems feed bottles onto a secondary conveyor line for further operations like filling or labeling.
- Manufacturing: Facilitating the assembly process by organizing parts in a precise order for assembly line workers.
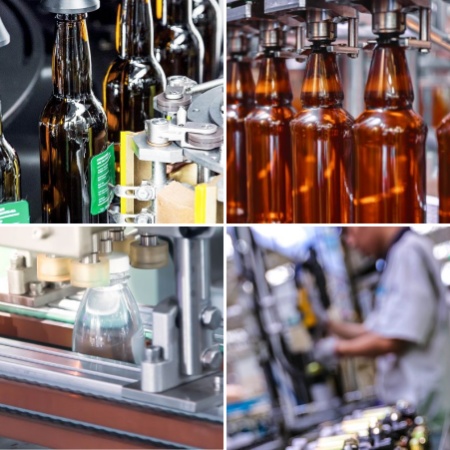
Design considerations for a stainless steel table
Designing an effective turntable feeding system requires considering the following:
- Load capacity: Ensuring the turntable can handle the weight and size of products.
- Durability: Choosing materials that can withstand operational demands and environmental conditions. Utilizing a stainless steel table can enhance durability and functionality, especially in industrial applications like feeding bottles onto conveyor lines.
- Precision: Selecting motor and control systems that offer the necessary precision for specific applications.
Turntable feeding vs. horizontal feeding
Turntable feeding systems are often compared to horizontal feeding systems. While both serve to automate the movement of products:
- Turntable feeding: As a table, it offers a compact solution that can be easily integrated into existing spaces without extensive modifications. It facilitates the continuous feeding of items into subsequent machinery, minimizing jams and optimizing workflow. It’s particularly effective for circular motion and where space is at a premium.
- Horizontal feeding: Typically involves conveyor belts moving products in a straight line and is suited for longer distances and larger-scale operations.
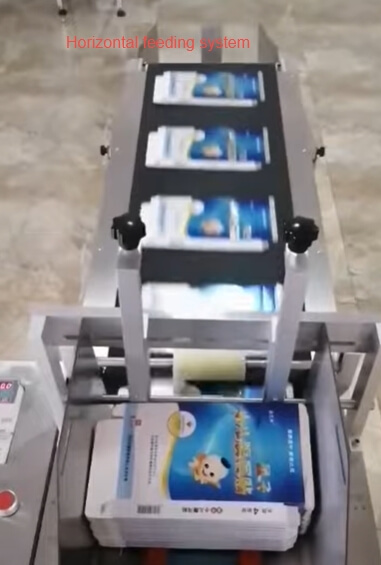
Advantages of turntable feeding
- Efficiency: Increases throughput by automating the movement and positioning of products.
- Accuracy: Reduces human error with precise placement and rotation.
- Versatility: Easily adapts to different products and packaging types with minimal adjustments.
- Guaranteed: Our turntable feeding systems come with guaranteed quality and performance, including robust after-sales service and a two-year guarantee on machine quality under stable conditions.
Challenges in implementation
- Mechanical wear: Regular maintenance is required to prevent downtime.
- Integration complexity: Integrating with existing systems may require customization and technical expertise.
- Cost: Initial setup and ongoing maintenance can be significant, depending on the system’s complexity.
Future trends
Innovation in turntable feeding technology is likely to focus on:
- Integration of AI and IoT: Enhancing the smart capabilities of systems for better diagnostics and adaptability.
- Improved durability: Developing materials and designs that extend life and reduce the maintenance needs of turntable systems.
Conclusion
As industries continue to seek efficiencies in production, turntable feeding systems stand out as crucial components in modern manufacturing environments.
Their ability to adapt to different operational needs while maintaining high standards of precision and efficiency makes them invaluable.
Future developments are expected to enhance their functionality, ensuring they remain integral to industrial automation.
As a company specializing in the production of pharmaceutical labeling equipment, Viallabeller’s machines are also equipped with turntable feeding systems. Here are some of the common labeling solutions we have for the pharmaceutical field: