Tablet manufacturing is a meticulous process that transforms raw materials into lifesaving medications. This intricate procedure ensures consistent quality, dosage, and effectiveness in each and every tablet produced.
Next, let’s describe the process.
The key points of tablet manufacturing
- The primary manufacturing processes for tablet production include wet granulation, dry granulation, and direct compression, each suited to different types of active pharmaceutical ingredients (APIs).
- The choice of manufacturing process depends heavily on the physical and chemical stability of the APIs, as these characteristics can significantly affect the outcome of the production.
- Essential equipment for successful tablet manufacturing encompasses granulators for particle size enlargement, mixers for blending ingredients, dryers to remove moisture, and coating machines for tablet finishing.
- Despite utilizing the correct machinery and processes, several common defects such as chipping, sticking, capping, and lamination can still occur, potentially compromising tablet integrity and efficacy.
It is crucial to implement rigorous quality control measures throughout the manufacturing process to detect and mitigate these defects, ensuring the high quality of the final pharmaceutical product.
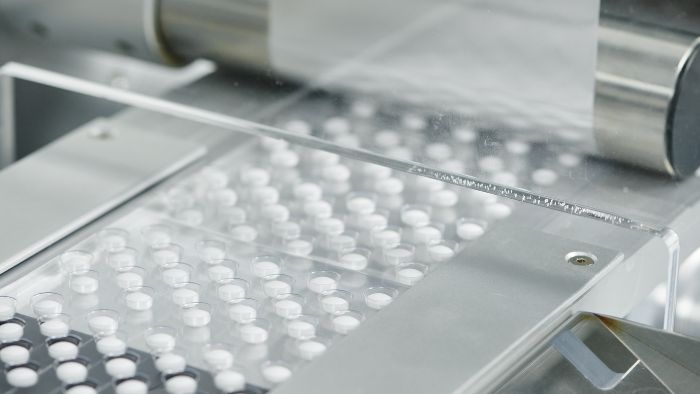
Tablet manufacturing process objectives
There are several objectives to strive for during the tablet manufacturing process:
- Develop tablets that possess sufficient strength and hardness to endure mechanical shocks encountered during manufacturing, packaging, transportation, and dispensing without degradation.
- Formulate tablets to ensure uniformity in weight and consistency in drug content across batches, maintaining precise dosage levels.
- Manufacture products with optimal bioavailability that meet the therapeutic requirements specified for their intended use.
- Create tablets that are chemically and physically stable, capable of retaining their integrity and efficacy over extended periods.
- Produce defect-free tablets that exhibit an aesthetically pleasing and professional finish to enhance consumer trust and compliance.
- Implement stringent quality control protocols to consistently achieve these standards while minimizing production errors and maximizing product reliability.
Types of tablet manufacturing process techniques
Tablet manufacturing involves various techniques to produce oral solid dosage forms, ensuring the tablets meet the required quality and efficacy standards.
The most commonly employed tablet manufacturing process techniques include:
Wet granulation
Wet granulation is a widely used method in tablet production that involves particle size enlargement and the use of a binding agent, enhancing the physical properties required for robust tablet formation. Here are the detailed steps and their purposes in a successful wet granulation process:
- Weigh, mill, and mix APIs with excipients: Start by accurately weighing the active pharmaceutical ingredients (APIs) and excipients. Mill them to achieve the desired particle size, then mix thoroughly to ensure a uniform distribution. This step is crucial for consistency in drug content and dosage.
- Prepare the binder solution: Create a liquid binder solution, which will act as an adhesive to hold the powdered ingredients together. The choice of binder affects the tablet’s dissolution rate and overall stability.
- Mix binder solution with powders: Gradually add the binder solution to the powder mix to form a wet, homogeneous mass. This mixing ensures that each particle of the powder is evenly coated with the binder, aiding in granule formation.
- Wet screening: Pass the damp mass through a mesh screen to form pellets or granules. This step controls the granule size, which is essential for uniform compaction and content uniformity in the final tablets.
- Dry the moist granules: Spread the granules and dry them to remove excess moisture. Proper drying is vital to prevent the degradation of sensitive ingredients and to achieve the right moisture content for compression.
- Dry screening to size granulation: Once dry, screen the granules to ensure consistent size. This uniformity is critical for even flow and compression during tablet formation.
- Mix dried granules with lubricants and disintegrants: Add lubricants to reduce friction during tablet compression, and disintegrants to ensure that the tablet dissolves appropriately upon ingestion. Mixing must be done carefully to avoid over-mixing, which can affect the tablet’s efficacy.
- Compress the granules into tablets: Finally, compress the prepared granules into tablets using a tablet press. This step transforms the granules into a solid and compact form, creating the final dosage form that is easy to handle, dose, and consume.
Dry granulation
Dry granulation is a method that compacts powder mixtures into larger pieces or compacts, which are then broken down into granules.
This technique is particularly beneficial when tablet excipients inherently possess binding properties and are advantageous for drugs that are sensitive to heat or moisture. The dry granulation process simplifies production by eliminating the need for wetting and drying steps.
Here are the steps and their purposes for a successful dry granulation tablet manufacturing process:
- Weigh and mill formulation ingredients: Start by accurately weighing the drug substances and excipients. Milling these ingredients to the proper particle size is crucial for uniform mixing and compaction. This ensures consistent dosage and stability in the final product.
- Mix the milled powders: Thoroughly mix the milled ingredients to achieve a homogeneous mixture. This step is essential for ensuring that each tablet contains the correct amount of active pharmaceutical ingredient (API).
- Compress the mixed powders into slugs: Use a heavy-duty press to compact the mixed powders into slugs. Compaction is necessary to create a dense mass that can be granulated in the next step. This process helps in binding the particles together without the need for additional binders.
- Mill and sieve the slugs: Break down the compacted slugs into granules by milling them. Sieving ensures granules are uniform in size, which is vital for consistent flow properties during the final compression into tablets.
- Compress them into tablets: Finally, compress the granules into tablets using a tablet press. This step transforms the granules into a final dosage form, providing the necessary compactness and hardness for the tablets to withstand handling and distribution.
Direct compression
The direct compression method involves compressing powdered materials into tablets without altering their physical properties. This approach is particularly cost-effective and widely used for manufacturing generic pharmaceutical products. It efficiently circumvents the challenges associated with both wet and dry granulation techniques.
Here are the detailed steps and their purposes in a successful direct compression tablet manufacturing process:
- Mill therapeutic agents and excipients: Begin by milling the active pharmaceutical ingredients (APIs) and excipients to achieve a consistent particle size. This step ensures a uniform blend and optimal compaction characteristics, crucial for tablet quality.
- Mix the milled powders, disintegrants, and lubricants: After milling, thoroughly mix the powders along with disintegrants and lubricants. Disintegrants are added to facilitate the tablet disintegration after ingestion, ensuring proper drug release and absorption. Lubricants are used to prevent the mixture from sticking to the equipment during compression, which enhances the manufacturing efficiency and tablet quality.
- Compress the tablets: The final step is to compress the well-mixed powders into tablets using a tablet press. This compression step forms the powders into a cohesive and compact solid dose form, ready for packaging and distribution.
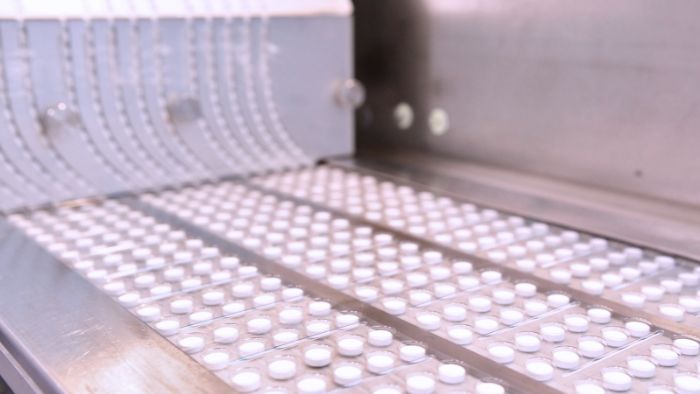
Influential factors in choosing a tablet manufacturing process
Several factors are critical when selecting the appropriate tablet manufacturing process:
- Compression properties of the API: The ability of your active pharmaceutical ingredients (API) to be compressed into a stable and effective tablet form is fundamental. APIs with good compression properties are more likely to produce high-quality tablets using simpler techniques like direct compression.
- Physical and chemical stability of the API: The API’s stability during processing is crucial. If an API is sensitive to heat or moisture, techniques like dry granulation or direct compression may be preferable to avoid degradation.
- Particle size of formulation ingredients: The particle size of APIs and excipients affects the uniformity of the mix and the compaction characteristics of the tablet. Properly sized particles enhance blend uniformity and tablet integrity.
- Availability of required processing equipment: The choice of manufacturing process often depends on the types of equipment available. For instance, if high-shear granulators are not available, wet granulation may not be feasible.
- Cost to manufacture: Economic considerations are always important. Processes that require fewer steps and less energy consumption, like direct compression, are generally more cost-effective, especially for high-volume production.
- Regulatory requirements: Compliance with regulatory guidelines can influence process selection. Certain processes may be preferred based on the ability to consistently meet regulatory standards for product safety and efficacy.
- Production scalability: The ability to scale the manufacturing process from pilot batches to full-scale production without significant changes to the process or product quality is essential, especially for mass-market pharmaceuticals.
Types of equipment used in tablet manufacturing
In the pharmaceutical industry, a diverse array of specialized machinery is essential for efficient tablet production. This encompasses a broad spectrum of equipment, each tailored for specific stages of the manufacturing process.
Coating and polishing machines are used to apply various coatings, including sugar coating, which enhances the taste, appearance, and stability of tablets.
Size reduction equipment
Various milling devices are pivotal in the tablet manufacturing process for reducing particle size. These include hammer mills, vibration mills, pin mills, end-runner mills, edge-runner mills, cutter mills, and ball mills.
Weighing balance machinery
Precision in tablet weight is achieved using different types of weighing balances. Options range from bulk systems to highly sensitive electronic weighing balances, ensuring precise measurements for quality control.
Granulators
Essential for creating tablet granules, granulators can operate in either wet or dry modes. Types include rotating-shape granulators, mechanical agitator granulators, high-shear granulators, fluidized-bed granulators, and dry granulators.
Mixing equipment
To ensure the homogeneity of tablet ingredients, various mixing machines are used. These include pneumatic mixers, diffusion mixers, convective mixers, ribbon blenders, orbiting screw mixers, horizontal blenders, and planetary blenders.
Drying equipment
Reducing moisture content in pharmaceutical powders and granules is crucial, facilitated by equipment like spray dryers, rotary dryers, and fluidized bed dryers.
Tableting machinery
Also known as tablet presses, these machines compress pharmaceutical powders into uniform tablets. High-speed rotary tablet machines and multi-layer rotary tablet presses are commonly used for efficient and quality tablet compression.
Coating and polishing machines
Tablet coating systems and polishing machines are used to apply a thin coating solution to tablets, enhancing their appearance and masking flavors, as well as extending their shelf life. These machines can apply various coatings, including sugar coating, which enhances the taste, appearance, and stability of tablets.
Packaging machinery
After production, tablets are packaged using sophisticated equipment that ensures protection and compliance with regulatory standards. Technologies include blister pack machines, pouch filling machines, and sachet packaging machines, each designed for specific packaging needs.
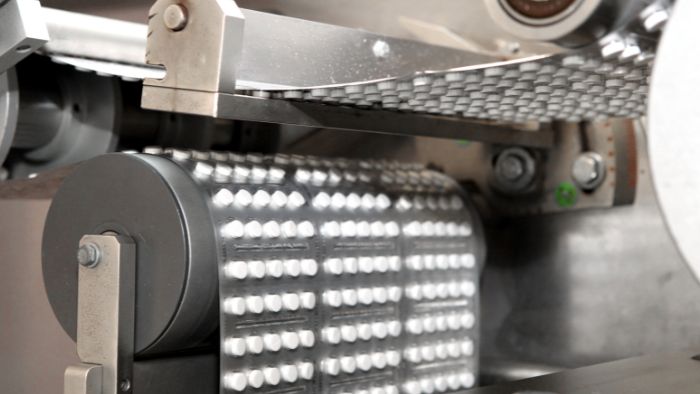
Labeling machines
Labeling equipment plays a crucial role in the tablet manufacturing process, providing essential information on packaging. Automatic label applicators, inline labeling machines, and rotary labeling systems ensure labels are accurately and efficiently applied to various types of pharmaceutical packaging.
Viallabeller’s labeling machines can provide pharmaceutical labeling equipment that can provide pill box labeling, and pill bottle labeling solutions ……
Common defects in tablet manufacturing and prevention strategies
During the tablet manufacturing process, even with the correct equipment in place, several common defects can occur that impact the quality of the final product, leading to poor tablet quality:
Capping
This defect typically manifests during the tablet compression phase, but it is often not detected until the coating stage. It involves the upper part of the tablet separating from the main body, which can lead to broken tablet pieces or bumps visible in the coating.
Chipping
Chipping frequently occurs due to excessive attrition during the coating process, where the edges of the tablets become damaged, leading to loss of material from the tablet’s surface.
Sticking and picking
These issues are prevalent in tablet production and can arise from several factors such as inadequate tablet formulation, over-wetting of the granules, or insufficient drying. Sticking refers to tablets adhering to the die walls, while picking involves material being pulled from the tablet surface, creating pits or imperfections.
Lamination
Lamination is similar to capping but involves separation along the horizontal plane of the tablet, typically caused by air entrapment during compression.
Mottling
Mottling is an uneven distribution of color on a tablet, which can be due to a variety of factors, including unequal distribution of materials in the blend or issues during the mixing process.
Implementing precise control over each step of the manufacturing process and using high-quality machinery tailored to the specific needs of the tablet formulation can prevent these defects. Regular maintenance of equipment and thorough training of personnel are also crucial in minimizing the occurrence of these common tablet defects.
In summary
Successful tablet manufacturing relies on a well-defined process and the right equipment. Choosing between wet, dry, or direct compression techniques depends on the characteristics of the active ingredients and desired outcomes.
Quality control is paramount throughout production to ensure consistent tablet properties and prevent defects like capping, chipping, sticking, or lamination.
By meticulously managing each stage, manufacturers can deliver high-quality pharmaceutical products through this intricate process of tablet manufacturing.
References and citations
- Oscar-Rupert Arndt, Impact of Different Dry and Wet Granulation Techniques on Granule and Tablet Properties: A Comparative Study, Journal of Pharmaceutical Sciences, Volume 107, Issue 12, December 2018, Pages 3143-3152,doi:https://doi.org/10.1016/j.xphs.2018.09.006
- Compressed tablets by direct compression