The ribbon printing system is an integral part of modern industrial printing solutions. In an era where precision and efficiency are paramount, this system offers unmatched versatility and reliability.
Ribbon printing systems are also widely used in creating personalized ribbon designs for gift wrapping, enhancing the aesthetics of gift presentations and packaging solutions.
From pharmaceutical packaging to food labeling, ribbon printing systems play a crucial role in ensuring that products are accurately and clearly labeled, meeting both regulatory standards and consumer expectations.
This guide explores the working principles, applications, advantages, and future trends of ribbon printing systems, providing a comprehensive understanding of their role in the labeling industry.
Working principles of ribbon printing systems
Ribbon printing systems are composed of several key components:
- Print head: The core of the system, is responsible for transferring ink from the ribbon to the substrate.
- Ribbon: A thin film coated with ink, available in various types to suit different printing needs.
- Drive system: Ensures precise movement and positioning of the ribbon and substrate during the printing process.
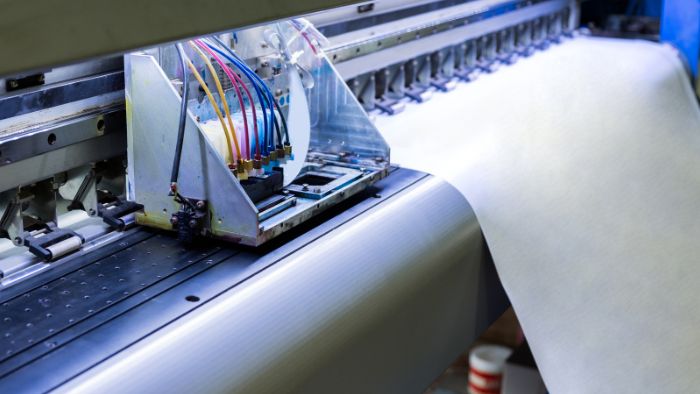
The printing process involves the interaction between the print head and the ribbon. The print head heats up specific points on the ribbon, causing the ink to transfer to the substrate in the desired pattern. The drive system maintains the correct tension and alignment, ensuring high print accuracy. Additionally, hot stamping can be used to apply foil to create decorative ribbons, enhancing the visual appeal for applications like awards and gift packaging.
Various types of ribbons are used, including thermal transfer ribbons, which are ideal for durable, high-quality prints, and thermal ribbons, which are suitable for short-term labeling needs. The system also supports multi-color printing, allowing for the production of vibrant, multi-colored ribbons in a single pass, which is both efficient and cost-effective.
Applications of ribbon printing systems in labeling machines
Ribbon printing systems are seamlessly integrated into various types of labeling machines:
- Automatic labeling machines: Used in high-speed production lines for consistent, high-volume labeling.
- Semi-automatic labeling machines: Ideal for medium-volume production with some manual intervention.
- Manual labeling machines: Used in low-volume or specialized applications where flexibility is key.
These systems can print multiple ribbons simultaneously, enhancing efficiency in high-volume customization.
These systems find applications across multiple industries:
- Pharmaceutical industry: Ensures that labels on vials, bottles, and packaging are clear and legible, complying with strict regulatory standards. Our labeling machines and a range of solutions, such as wrap-around labeling solutions and horizontal labeling solutions, all use this system, which improves the efficiency of drug labeling without having to make labels first and then label.
- Food industry: Provides durable and readable labels that withstand various environmental conditions.
- Cosmetic industry: Delivers high-quality, aesthetically pleasing labels for product branding and information.
These systems also offer the capability to create and save unique ribbon designs tailored to customer needs, providing unlimited design possibilities and quick setup for future use.
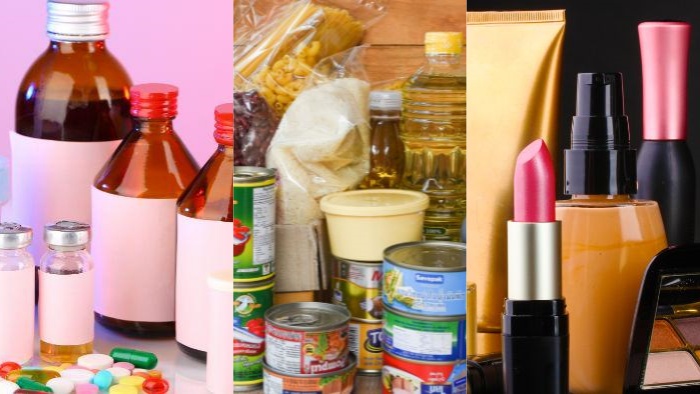
Advantages of ribbon printing systems in print quality
The ribbon printing system offers several significant advantages:
- High print accuracy and clarity: Ensures that every label is sharp and easily readable.
- Compatibility with various label materials: Works well with paper labels, transparent labels, and synthetic materials, providing flexibility in label design.
- Efficient printing speed: Meets the demands of high-speed production environments without compromising quality.
- Durability and longevity: Produces labels that resist smudging, fading, and abrasion, ensuring they remain intact throughout the product’s lifecycle.
- Scalability and flexibility: Easily adapt to different production volumes and label designs, making it suitable for a wide range of applications.
Using foil in the ribbon printing process enhances visual appeal and efficiency by enabling multi-color foil stamping and reducing material waste.
Ribbon printers are versatile, with various types like inkjet, thermal, and digital models tailored for specific printing needs and applications.
Maintenance and care of ribbon printing systems
Proper maintenance is crucial to ensure the longevity and performance of ribbon printing systems:
- Daily maintenance: Includes cleaning the print head to prevent ink buildup and ensure consistent print quality.
- Ribbon replacement: Timely replacement of used ribbons to avoid print defects and ensure continuous operation.
- Common troubleshooting: Addresses issues such as unclear prints, ribbon breakage, and label detachment with practical solutions.
- System upgrades and optimization: Regular updates to the control software and hardware components to enhance performance and integrate new features.
Using a USB cable is essential for connecting the ribbon printing machine to a computer, allowing for designing and printing custom ribbons directly from a PC.
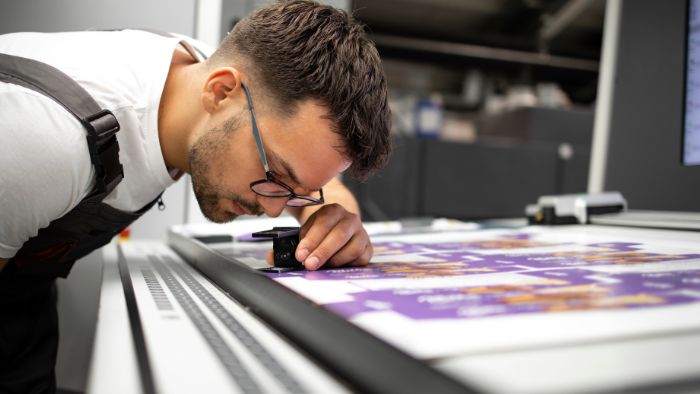
Future trends in ribbon printing systems
The future of ribbon printing systems is marked by several exciting developments:
Technological innovations: Advancements in high-resolution print heads and intelligent control systems enhance print quality and operational efficiency. Modern ribbon printing machines offer high print quality and ease of use, making them ideal for various applications including packaging materials.
Environmental and sustainability considerations: The use of eco-friendly materials and energy-efficient technologies aligns with growing environmental concerns and regulatory requirements. Additionally, these systems are highly compatible with polyester single/double-faced satin ribbon, making them suitable for custom designs and efficient production.
Conclusion
In conclusion, the ribbon printing system is an indispensable tool in the industrial printing landscape. Its ability to deliver high-quality, durable labels across various applications makes it a valuable asset for businesses aiming to enhance their labeling processes.
As technology advances and sustainability becomes increasingly important, ribbon printing systems will continue to evolve, offering even greater efficiency and versatility.
By understanding their principles, applications, and maintenance, companies can leverage these systems to achieve superior labeling results and maintain a competitive edge in the market.