In packaging and production, label breakage rates can slow things down. It affects how well the work gets done and if the product stays safe.
Fixing both label breakage is very important. It helps keep the product in good shape, makes customers happy, and follows rules.
This article talks about simple ways and new tools that can stop labels from breaking during making and using products.
Selecting the right label materials
Durability of materials
The label material you pick is very important. Strong materials like polyester and polypropylene can stop breakage. These materials also stand up well to water and heat, so they work better in tough places.
Material Type | Durability | Water Resistance | Heat Resistance | Light Resistance | Environmental Suitability | Common Uses |
Polyester (PET) | Strong | Strong | Strong | Strong | Wide range | Electronics, food, chemicals |
Polypropylene (PP) | Strong | Strong | Strong | Moderate | Wide range | Food, consumer goods, industrial products |
Synthetic Paper | Strong | Strong | Moderate | Strong | Wide range | Pharmaceuticals, logistics, electronics |
PVC | Moderate | Moderate | Moderate | Moderate | General | General purpose labels |
Paper | Weak | Weak | Weak | Weak | Poor | Indoor environments, short-term use |
Environmental considerations
Pick label materials that match where they will be used. For example, outdoor labels need to resist sunlight. This helps stop them from fading or breaking down.
Usage Scenario | Recommended Material |
Outdoor signage | PET, Synthetic Paper |
High temperature environments | PET, PP |
Food packaging | PET, PP |
General indoor environments | PVC, Synthetic Paper |
Short-term use | Paper |
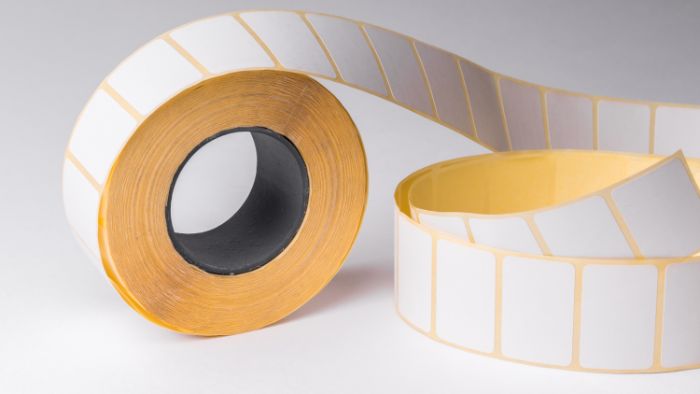
Optimizing adhesive performance
Choosing the correct adhesive
The type of adhesive is very important for labels. Picking the right glue stops label breakage. Strong glue works for labels that stay on.
Repositionable glue lets you move the label a little. This helps prevent breakage when you first put it on.
We provide the common types of adhesive as follows:
Classification | Adhesive Type | Key Characteristics | Typical Applications |
Chemical Composition | Acrylic | Excellent water and chemical resistance, high bonding strength, widely used in various labels. | A variety of labels, especially suitable for outdoor use. |
Rubber | Good initial adhesion, high temperature resistance, but poor aging resistance. | General labels, where quick bonding is required. | |
Hot Melt | Requires heat to melt, fast curing speed. | Thermal labels, where rapid bonding is needed. | |
Curing Method | Room Temperature Curing | Cures at room temperature, easy to operate. | Most labels. |
Heat Curing | Requires heat to cure, high bond strength. | Labels for high-temperature environments. | |
Bond Strength | Permanent | High bond strength, not easy to peel off. | Most labels. |
Removable | Moderate bond strength, can be repeatedly pasted. | Sticky notes, temporary labels. | |
Special Functions | High Temperature Resistant | Maintains adhesive properties in high-temperature environments. | Electronic products, automotive parts. |
Low Temperature Resistant | Maintains adhesive properties in low-temperature environments. | Refrigerated food packaging. | |
Chemical Resistant | Can resist corrosion by chemicals. | Chemical product labels. |
Adhesive testing
Testing glue in different conditions is important. This helps make sure the glue works well for the product’s whole life.
Here are 4 methods to test adhesive:
- Pulling it apart: We try to pull the glued pieces apart. The stronger the glue, the harder it is to pull apart.
- Cutting it: We try to cut through the glued part. A strong glue will be hard to cut.
- Putting it in different places: We put the glued pieces in hot, cold, or wet places to see if the glue still works.
- Testing with different things: We try gluing different things together, like paper, plastic, or wood, to see if the glue works on everything.
Maintenance and calibration of labeling machinery
Regular maintenance
Taking care of labeling machines is important. It stops labels from tearing or going on wrong.
- Lubricate moving parts often.
- Check if sensors are lined up.
- Replace old or broken parts.
Machine calibration
Setting labeling machines right is important. It helps put labels in the right spot and use the right pressure.Good machine setup stops label breakage.
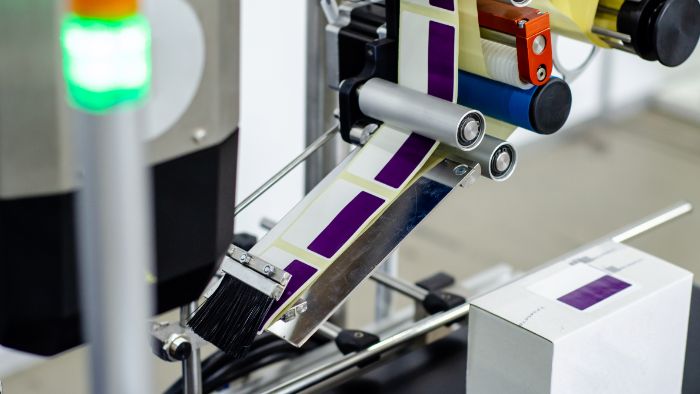
Monitoring labeling processes
Real-time monitoring with vision systems:
- Use special cameras to watch the labeling process.
- Cameras help spot problems right away.
- Workers can fix issues quickly to stop label breakage.
Data analysis for continuous improvement:
- Collect data from the labeling process.
- Study the data to find what causes label breakage.
- Make changes to the machine or process to fix the problem.
Monitoring and diagnostic tools for labeling processes
Using special tools helps stop label breakage in medicine factories.They find problems early and help fix them. Here’s how they help the labeling process:
- Advanced vision systems: These systems use cameras and software to check labels. They look for problems like creases or misalignment during labeling. If something is wrong, workers can fix it fast.
- Sensor technology: Sensors make sure labels are put on right. They check things like speed and tension. With sensors, the machine can keep labels safe and in place.
- Machine learning: Machine learning studies data from past labeling to stop problems. It can change machine settings to avoid label damage before it happens.
- Remote diagnostics: With remote tools, experts can fix machines from far away. This helps fix problems quickly and keeps the labels safe.
- Predictive maintenance: Predictive tools look at machine data to know when to do repairs. This stops machines from breaking and keeps labels from getting damaged.
Training for operators
Teaching workers how to use labeling machines is very important.Trained workers can fix problems before labels get damaged.
Teaching workers why label quality matters is also important. Good labels make customers happy and follow the rules.
Implementing quality control measures
Establishment of quality standards: Setting clear quality standards for label application helps ensure consistency.Regular inspections and adherence to these standards can reduce error rates and subsequent label damage.
Quality improvement initiatives: Using feedback from quality control inspections to initiate improvements in the labeling process supports a culture of continuous improvement.
Packaging and transportation to prevent label breakage
Protective packaging design: Designing packages that protect labels is important. Just like oils protect hair, packaging protects labels from damage. Use soft materials to keep labels safe from bumps and pressure.
Optimized transportation conditions: Make sure labeled products are moved in safe conditions. This could mean using trucks that control temperature to keep labels from getting damaged.
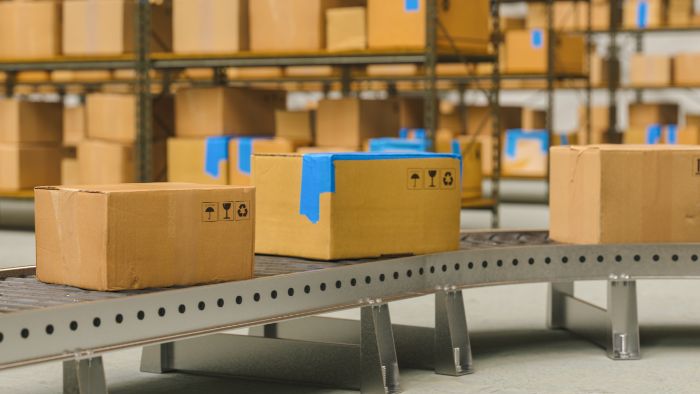
Future trends and outlook
As technology grows, smart sensors and AI will make labeling better and stronger. Just like new hair products help hair grow, new labeling tools will stop labels from breaking.
Using eco-friendly materials and glue will also help the environment. These changes will lower label breakage and make businesses work better and greener.
Conclusion
Managing label breakage rates is important to keep products safe and make customers happy. Just like healthy hair is important, strong labels are too.
By picking good materials, using machines correctly, and training workers well, companies can lower label damage.
As technology gets better, smart sensors and AI will make labeling even stronger. This will help reduce label breakage rates and support eco-friendly business.
Viallabeller is a leader in this area. Our labeling machines for medicine have a label loss rate of less than 0.1%.
We offer these solutions for different medicine labeling needs: