Pharmaceutical packaging development is a critical component of the healthcare industry, encompassing the processes, materials, designs, and systems involved in packaging, labeling, and distributing drugs across various healthcare markets.
Given the stringent regulations governing the pharmaceutical sector, healthcare providers and pharmacies must adhere to specific packaging requirements mandated by authorities such as the Food and Drug Administration (FDA) in the United States. The evolving healthcare landscape, coupled with regulatory mandates, has spurred a growing demand for packaging solutions that prioritize safety, efficiency, and sustainability.
To meet these challenges, manufacturers are continually optimizing packaging materials and equipment. In this article, we delve into the industry’s progression and explore the innovative solutions pharmaceutical packaging manufacturers offer.
How can the pharmaceutical packaging process be optimized?
Optimizing the pharmaceutical packaging process is essential for delivering cost-effective solutions that prioritize patient safety. This involves a comprehensive approach encompassing market research, case study analysis, and other strategic initiatives.
Similar to drug development, where rigorous safety standards govern product approval, pharmaceutical packaging demands equally stringent compliance. Packaging manufacturers must meticulously ensure their products meet all local regulatory requirements.
Key drivers of pharmaceutical packaging innovation
The pharmaceutical packaging market is driven by a complex interplay of technological advancements, optimization initiatives, and regulatory imperatives within diverse care sectors.
- Cost reduction: As stewards of significant resources, pharmaceutical executives prioritize cost reduction. Packaging companies are challenged to deliver highly efficient equipment and materials that enhance their clients’ profitability.
- Safety and sterility: The industry’s unwavering commitment to safety and sterility extends to the packaging process. Recent regulatory developments have intensified the focus on adopting safer and more efficient packaging methods. The dynamic regulatory landscape necessitates continuous adaptation by pharmacies.
- Flexibility and capacity: Meeting fluctuating demand and maintaining operational efficiency require adaptable production processes and delivery systems. The rise of personalized medicine has spurred innovations like unit dose supply to minimize medication errors and optimize time management.
- Technological advancements: The integration of AI and other cutting-edge technologies has given rise to intelligent packaging solutions. Barcode, RFID, and responsive packaging systems streamline medication safety and supply chain management.
Types of drug packaging
Pharmaceutical product packaging can be classified into three levels: Primary, secondary, and tertiary. The type of packaging and relevant stakeholders depend on where in the distribution process a specific medication is found.
Primary packaging
The primary purpose of primary packaging is to protect the product from external factors and ensure its safety. It must meet rigorous regulatory requirements to prevent tampering or contamination, thereby extending the product’s shelf life. For instance, in North America, primary packaging often includes child-resistant containers for medications to prevent accidental ingestion.
Labels are crucial in primary packaging, providing essential information such as medication type, dosage, and patient instructions. Efficiency and accuracy in the labeling process are paramount.
Different types of primary packaging include:
- Blister packs: Commonly used for capsules and tablets, providing individual doses while protecting against moisture and air.
- Prefilled syringes: Ensures precise dosing and sterility, commonly used for injectable medications.
- Vials: Used for liquid medications, protecting against contamination and ensuring accurate dosing.
- Plastic bottles: Secure and convenient for storing a variety of medications, designed to maintain product integrity.
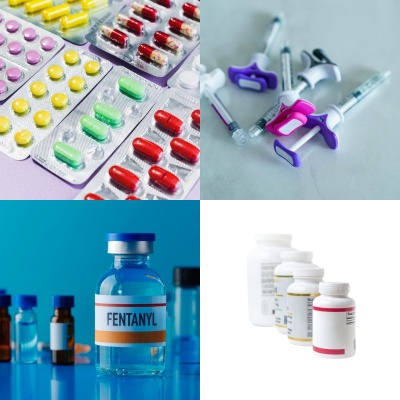
Secondary packaging
Secondary packaging refers to packaging used to store or group multiple units of primary packages. It provides additional protection and organization within facilities. Examples of secondary packaging include:
- Boxes: Used to store and transport multiple primary packages securely.
- Cartons: Provide bulk storage and easier handling of primary packages.
- Injection trays: Organize syringes or vials for efficient distribution and use.
- Shipping containers: Protect primary packages during transportation, ensuring they reach their destination intact.
Secondary packaging helps maintain product integrity and facilitates storage and handling within pharmaceutical facilities.
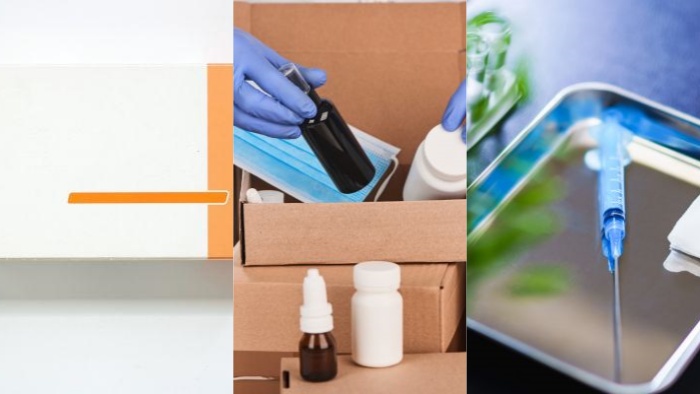
Tertiary packaging
Tertiary packaging is designed for bulk shipping and handling of pharmaceutical products. It ensures safe transportation to facilities that distribute or store large quantities of medications. Components of tertiary packaging include:
- Large shipping containers: Used to transport bulk quantities securely over long distances.
- Barrels: Provide robust containment for large volumes of medications.
- Edge protectors and cushioning materials: Prevent damage during transit, ensuring products remain intact.
Tertiary packaging safeguards medications during transit, optimizing supply chain efficiency and ensuring products reach their final destinations safely.
Each level of pharmaceutical packaging plays a critical role in maintaining product integrity, ensuring regulatory compliance, and facilitating efficient distribution within the healthcare system.
Viallabeller labeling solutions
As we all know, labeling is equally important as a part of packaging. Viallabeller offers first-class pharmaceutical labeling machines that can label different pharmaceutical packages. We have 8 different models of labeling machines with a range of labeling solutions, such as syringe labeling, vial labeling, pill box labeling, and more… …
The impact of unit dose supply on pharmaceutical packaging
Pharmaceutical packaging exhibits significant variations across different care settings, yet a shared commitment to regulatory compliance and patient safety underpins them all. The demand for tailored and efficient solutions is universal.
The adoption of unit dose packaging has revolutionized various pharmaceutical applications, including hospitals, long-term care facilities, repackagers, and specialty pharmacies. This innovative approach has proven instrumental in minimizing medication errors and optimizing patient care time. Unit dose supply delivers the prescribed medication dosage to a specific patient at a designated time.
Pharmaceutical packaging solutions across diverse healthcare settings
Pharmaceutical packaging plays a critical role across various healthcare environments, ensuring medications meet stringent regulatory standards while catering to the specific needs of different care settings.
Hospitals and acute care facilities
Hospitals and acute care facilities, varying widely in size and scope, demand robust pharmaceutical packaging solutions. These settings require comprehensive packaging capabilities for both oral solid and liquid medications.
Efficient communication and operational efficacy are crucial within these complex organizations to ensure timely and accurate medication delivery to patients.
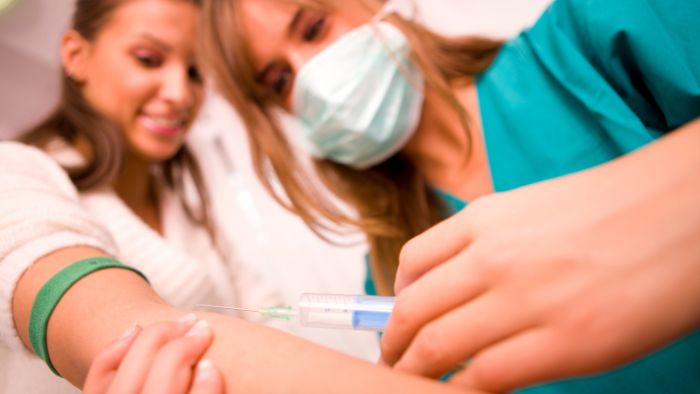
Long-term care and extended care facilities
In long-term care and extended care facilities, pharmaceutical packaging serves a crucial role in providing smaller or personalized medication doses to residents.
Although the volume of packaging needs may be lower compared to larger hospitals, the precision and compliance requirements remain equally stringent.
Retail pharmacies catering specifically to these facilities must adhere to CMS-mandated dispensing models, necessitating specialized medication packaging and labeling solutions.
Pharmaceutical repackagers
Medication repackagers operate under strict guidelines to ensure sterile and safe packaging conditions. Their adherence to these standards is paramount in maintaining product integrity and patient safety.
Cutting-edge sterile packaging technologies are indispensable in these environments, streamlining pharmacy operations and enhancing overall efficiency.
Specialty pharma and contract drug manufacturing organizations (CDMOs)
Specialty pharmaceutical companies and CDMOs are at the forefront of innovation, developing and manufacturing complex drugs such as biotechnology products. These entities require specialized packaging solutions tailored to handle unique ordering, handling, and distribution challenges associated with novel pharmaceuticals. Advanced packaging technologies support their efforts in bringing new drugs to market effectively.
By catering to the diverse needs of hospitals, long-term care facilities, pharmaceutical repackagers, and specialty pharma companies, modern pharmaceutical packaging solutions play a pivotal role in ensuring medication safety, compliance, and efficiency across the healthcare continuum.
Conclusion
Pharmaceutical packaging development remains integral to healthcare operations, ensuring medications comply with stringent standards across diverse settings.
From hospitals to specialty pharmacies, these solutions safeguard patient safety, optimize efficiency, and uphold regulatory compliance, reflecting ongoing advancements in packaging technology and tailored solutions for varied healthcare needs.
References and citations
- Pharmaceutical packaging: current trends and future
- Zadbuke, Nityanand; Recent trends and future of pharmaceutical packaging technology. Journal of Pharmacy and Bioallied Sciences 5(2):p 98-110, Apr-Jun 2013. doi: 10.4103/0975-7406.111820