Missing label detection is super important! Imagine sending out packages without any addresses. That’s what happens when labels go missing.
In factories that make and package products, special machines check every item to make sure it has a label.
This keeps everything organized and helps make sure customers get the right thing.
What is missing label detection?
Missing label detection is a tool employed in packaging area to find out products missing the necessary labels. It often involves measuring label dimensions to ensure accuracy and completeness.
Because it helps make sure the labels and the spaces between them are the right size. This helps keep quality control, especially when things are moving quickly in production.
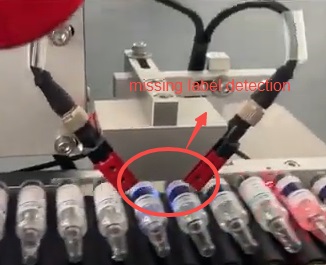
Functions of missing label detection
The importance of missing label detection can be explained with these key points:
For regulatory compliance
Many industries, like medicine, food, and cosmetics, have rules that say every product must have certain labels. These rules are very strict, and all products must have the correct label with the right information. If a product is missing a label, the company can get into big legal trouble.
Labels do more than give information; they also show the brand’s identity. For example, the label might have the company’s logo or special colors that people recognize. This helps customers stay loyal to the brand because they know which brand they are buying when they see the label.
For consumer safety
Labels are very important for keeping people safe. They often include key safety details, like how to use the product, what ingredients are in it, and warnings about things that may cause allergies. If a product doesn’t have a label, it can be dangerous, especially if it needs to be handled or used in a certain way.
Custom labels for products give these important details to keep consumers safe. They also help people compare different products and choose the right one. Without a label, a person might not know if a product is safe or if it has something they are allergic to.
For brand integrity
A brand’s reputation depends on having clear and correct labels on its products. If a product is missing a label, customers might feel upset or think the product is not safe. This can hurt the company’s reputation and make people stop trusting the brand. Good labels help show that the product is safe and reliable. Labels also help products stand out from others in the store.
When people shop, they look at labels to decide which product to buy. If a product doesn’t have a label, it might look less appealing, and people might choose another product. A strong label with clear, helpful information builds the brand’s identity and helps people decide what to buy.
For operational efficiency
Detecting missing labels early in the production process helps companies save time and resources. If a missing label is found early, the problem can be fixed before the product reaches the final steps of production or gets sent to stores. This helps the company save money and time, avoiding bigger problems later.
Systems that find missing labels can catch the problem while materials are still being worked on, making the whole process more efficient. For food products, labels not only give information—they also make the product more appealing.
A label with clear ingredient lists and marketing claims, like being organic or made with natural ingredients, can make customers more interested in buying the product. Good labels can even make people willing to pay more for a product because they believe it offers more value.
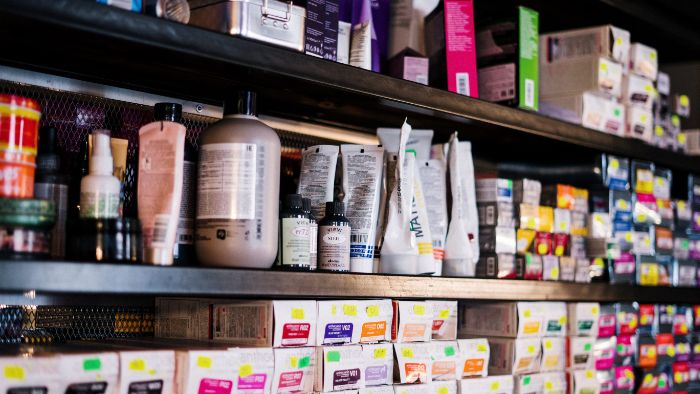
Technologies used in missing label detection
Different technologies are used to find missing labels, and each one works best for different types of packaging and production environments:
Vision systems
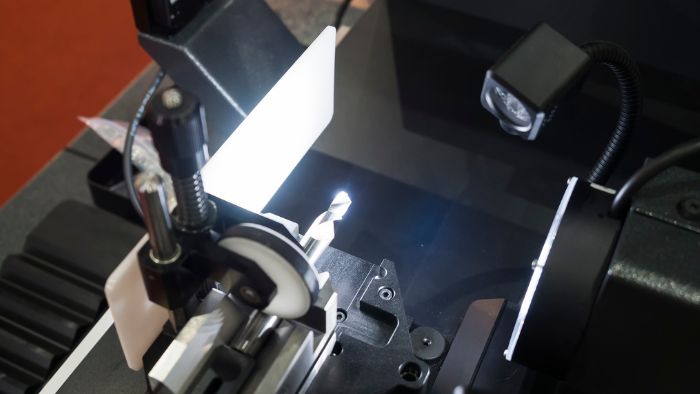
Vision systems use cameras and software to check products as they move along the production line. These cameras take pictures of the products and compare them to what the label should look like when it is in the correct place.
If a label is missing or not placed right, the system will signal a problem. This helps ensure products are labeled correctly before they are sold.
One type of label that works well with vision systems is called a pressure-sensitive label. These labels can be used on many types of packaging, like bottles, jars, and tubes. They stick to the product after a protective liner is removed, making them easy to apply during production.
Capacitive sensors
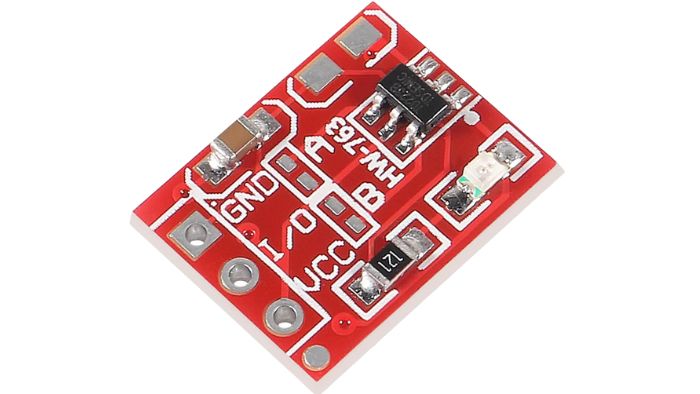
Capacitive sensors work differently. These sensors can tell if a label is there by measuring changes in the material on the product’s surface.
When a label is missing, the sensor can detect it because the material properties are different between the labeled and unlabeled areas. Capacitive sensors are useful for making sure labels are applied, even when products are moving quickly on the line.
Optical sensors
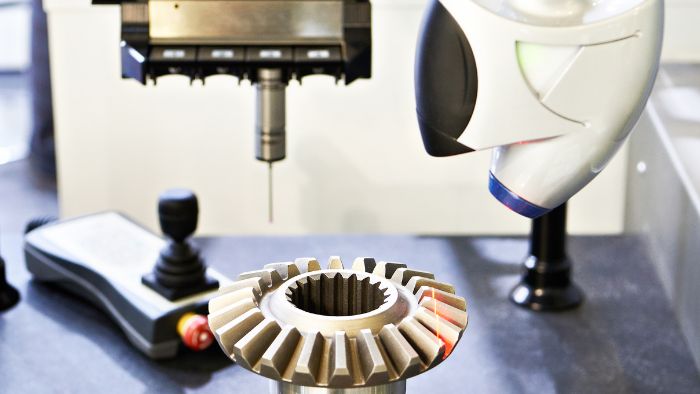
Optical sensors use light beams to find missing labels. These sensors shine light on a product and measure how the light reflects or passes through it. If a label is missing, the reflection will be different, and the sensor will detect the issue.
Optical sensors are good for catching small errors, like when a label is misaligned or partially missing. They are often used because they work fast and help catch mistakes early in production.
Ultrasonic sensors
Ultrasonic sensors are helpful for finding labels on clear materials. These sensors send out sound waves that humans cannot hear.
When the waves hit the product, they bounce back, and the sensor measures how they return. If a label is missing, the waves bounce back differently, showing that there is a problem. This technology works well for packaging made of see-through materials.
QR codes can also be added to labels to give customers more information. For example, scanning a QR code on a food label might provide a recipe or details about how the product was made.
Missing label detection bar
A missing label detection bar is a special tool made to find missing labels on materials that have been rewound, like rolls of packaging material.
This tool is small and fits well in tight spaces on the production line. It helps manufacturers find label problems before the materials are used to package products.
Challenges in missing label detection
Even with new technology, finding missing labels still has some problems:
- Fast production lines: Products move quickly, and it can be hard for systems to check each item, which can cause mistakes.
- Different packaging designs: Packages come in many sizes, shapes, and materials. There are also many types of labels. This makes it harder to check every label. Picking the right label is important for helping people know the product, making it stand out, and connecting with customers.
- Environmental factors: Things like dust and humidity can make it harder for sensors to work well. Systems need to be strong and checked often.
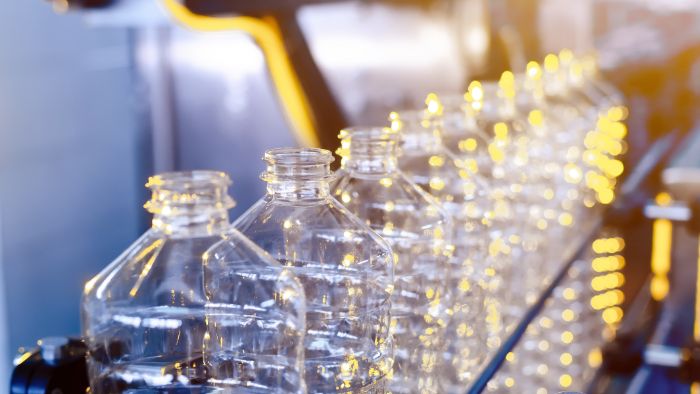
How to choose missing label detection
Identify needs
Decide what types of labels you need to check. Some systems work better for different kinds of labels.
Check accuracy
Look for systems that find missing labels correctly. Accuracy is important to avoid errors.
Consider speed
Choose a system that works fast. You want to detect missing labels quickly to keep things moving.
Review cost
Find out how much the system costs. Choose one that fits your budget while meeting your needs.
Ease of use
Select a system that is easy to use. It should be simple to set up and operate.
Look for support
Pick a system with good customer support. Help should be available if you run into problems.
Check compatibility
Make sure the system works with your existing equipment. It should fit well with what you already have.
Read reviews
Look at reviews from other users. Their experiences can show how well the system works.
Test the system
Try out the system before buying. Testing helps make sure it meets your needs.
Conclusion
Missing label detection is an important tool. It can make sure products are good in many businesses.
Viallabeller offers medicine labeling machines with missing label detection. They can label ampoules, syringes, vials, pill bottles, tubes, and other pharma devices.
FAQs
Q1: How do vision systems ensure the detection of missing labels?
Vision systems are like smart eyes that look at products as they are being made. They use special math to check if the labels are correct.
If a label is missing or wrong, the machine will know. The labels also have rules that tell the machine what to do next based on what the machine is doing.
Q2: Can missing label detection systems be integrated into any production line?
Definitely! Most machines that check for missing labels are like puzzle pieces that can fit into many different puzzles.
However, sometimes, a factory might have a unique puzzle, and the machine might need a few extra pieces to fit.
Q3: What steps should manufacturers take to maintain the accuracy of missing label detection systems?
Factories need to keep their label checking machines in good shape. They do this by checking them often to make sure they work right.
Sometimes, the machines need to be updated to work with new kinds of packages or follow new rules.
Q4: Are there any industries where missing label detection is more critical than others?
Companies that make things like food and medicine also need to put labels on their products.
These labels are like a secret code that tells people what’s inside.
Q5: What future advancements can we expect in missing label detection technology?
In the future, machines that check for missing labels might use AI and machine learning.
This means they could get even better at finding mistakes and could work with lots of different kinds of materials and packaging.
Plus, they’ll be tougher and won’t get messed up as easily when things like heat or cold change.