The manufacturing process of fully automatic labeling machines, particularly those designed for vials, involves a meticulous series of steps aimed at ensuring precision, reliability, and efficiency. This guide delves into the comprehensive stages involved in producing a Viallabeller labeling machine, from initial design to the final stages of assembly and testing.
Initial design and planning
- Design conceptualization: Every labeling machine begins with a detailed design process where engineers draft initial sketches and CAD models, considering customer feedback and regulatory requirements. These designs often include customer-specific solutions tailored to meet unique serialization and aggregation requirements.
- Material selection: Materials are chosen based on durability, cost-effectiveness, and suitability for the operational environment, with stainless steel often preferred for its hygiene and strength.
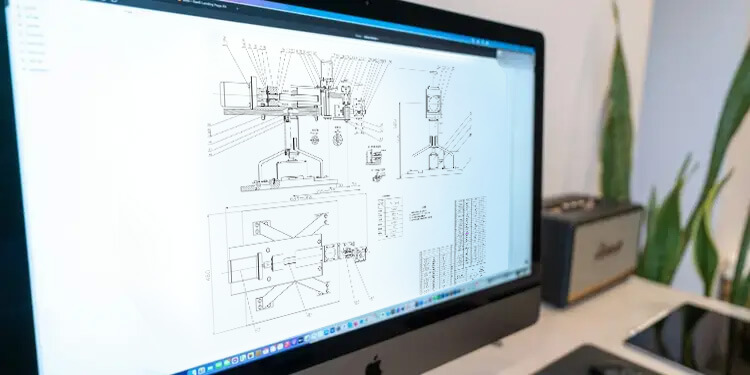
Component manufacturing
- Precision engineering: Components of labeling machines are manufactured with high precision using CNC machining, laser cutting, and other advanced fabrication technologies.
- Component assembly: Small components such as sensors, rollers, and labeling heads are assembled in controlled environments to prevent contamination and ensure high quality. Label applicators play a crucial role in this process by streamlining the application of labels, enhancing efficiency and product labeling quality.
Assembly of the labeling machine
- Frame construction: The main frame of the machine is assembled first, providing a stable base for other components.
- Installation of electrical systems: Electrical systems, which include wiring, sensors, and control panels, are installed to provide power and automation capabilities to the machine.
Software and labeling technology automation
- Software integration: Custom software is developed and integrated into the labeling machine to handle various labeling tasks and ensure flexibility in handling different vial sizes. Labeling technology plays a crucial role in this integration, enhancing the efficiency and sustainability of the labeling process across various industries.
- Automation testing: The machine undergoes several rounds of testing to ensure that all automated processes function correctly and meet predefined standards.
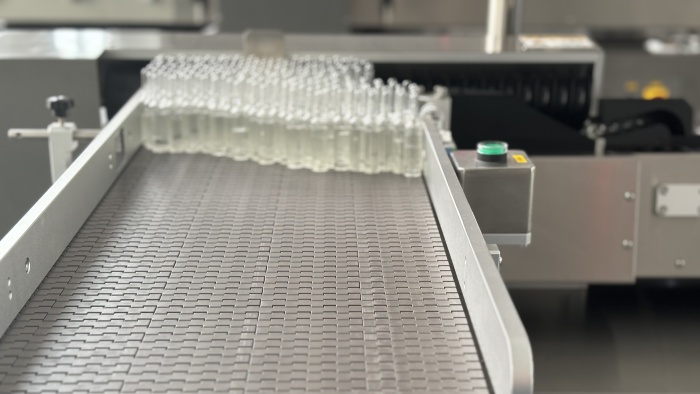
Quality control and testing
- Functional testing: Each labeling machine is tested to check its accuracy in applying labels to vials, ensuring that it meets industry standards for precision. Label printing plays a crucial role in this process, as it ensures that labels are printed correctly and applied accurately.
- Stress testing: Machines are also subjected to several hours of operation to identify any potential failures under continuous use.
Final assembly and quality assurance
- Final assembly: After testing, the final components such as housings and safety guards are installed. Labeling systems play a crucial role in this stage by ensuring labels are applied efficiently and accurately, enhancing overall productivity.
- Quality inspection: A final inspection is conducted to ensure that every aspect of the machine meets quality standards. Machines are reviewed for any aesthetic defects and operational inconsistencies.
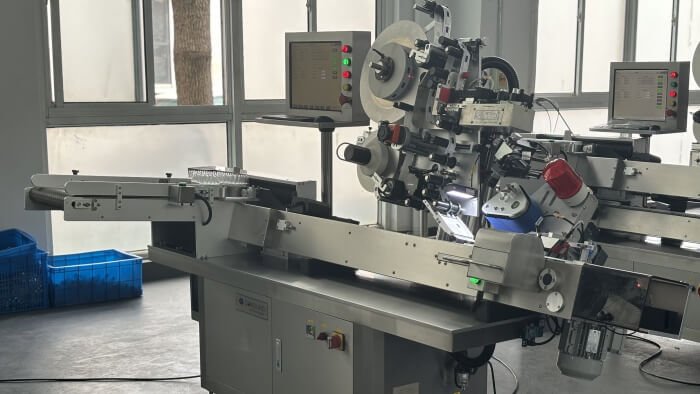
Packaging equipment and logistics
- Secure packaging: Each labeling machine is carefully packed to prevent damage during transportation. Specialized packaging materials are used to cushion the machine and protect sensitive components. Packaging equipment plays a crucial role in ensuring the safe transportation of these machines.
- Shipping arrangements: Logistics are arranged to ship the labeling machine to the customer, with all necessary documentation and handling instructions included to ensure a smooth installation process.
After-sales support for labeling systems
- Installation support: Technicians may be sent to assist with machine installation and calibration at the customer’s site.
- Training and maintenance: Customers receive training on operating the machine and scheduled maintenance is discussed to prolong the machine’s life and performance. The training also covers the use of the label printer, ensuring customers can efficiently handle label printing and dispensing systems for various industrial applications.
Conclusion
The manufacturing process of a Viallabeller labeling machine is a complex but well-orchestrated series of steps designed to deliver a product that meets the exact needs of pharmaceutical companies.
With an emphasis on precision, reliability, and customer satisfaction, Viallabeller ensures that each machine is built to the highest standards, ready to perform in high-stakes environments where accuracy is paramount.
This thorough manufacturing process not only underscores the company’s commitment to quality but also enhances the trust placed in its machines by customers worldwide.
We also offer a range of labeling solutions to our customers: