Label peel distance is the space between where a label lifts off its backing and where it sticks to the product.
This small gap is important for making sure the label goes on right and fast. Label peel distance can change how labeling machines work, from how well the label sticks to how quickly the machine works.
So, It is also important to know how the peel works. Special tools and machines measure and improve label peel distance for better results.
let us dive into:
Understanding labels peel distance and peel angle
Label peel distance is a planned measurement, not random. It depends on the label material, the sticky glue, and how fast the machine works.
This distance is important because it helps the label stick well. If the distance is too short or long, problems like bubbles or loose labels can happen.
The label material matters. Some are thick, thin, or more bendable. Each type needs a different peel distance to work right.
Thick labels need more peel distance. This gives them time to separate from the backing without problems.
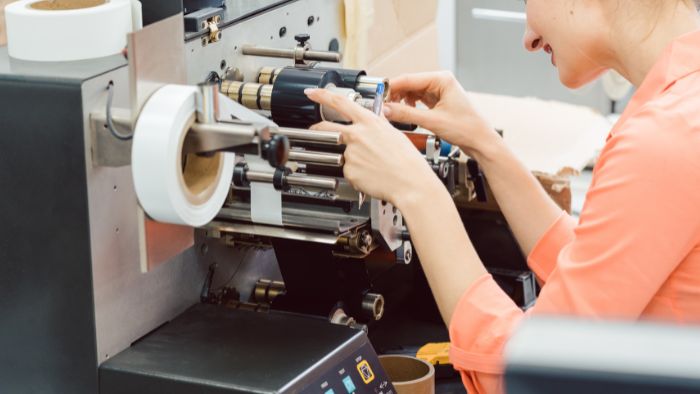
Factors influencing label peel distance and peel force
Several factors come into play when determining the optimal label peel distance for a particular application. These include:
Factor1-label material
The label’s thickness and flexibility matter. Thick labels may need more distance, while flexible ones may need less.
Factor2-adhesive type
The sticky glue also matters. Strong glue may need less peel distance. Weak glue may need more distance to stick well.
Factor3-label shape and size
Bigger or odd-shaped labels need good peel distance to stop wrinkles.
Factor4-labeling machines speed
Faster labeling machines need shorter peel distances. Slower machines may use longer peel distances.
Factor5-peel angle
A steep peel angle needs less distance. A flat peel angle needs more distance.
Viallabeller’s labeling machines can adjust speed for smooth label peeling. One of the best machines for tamper-evident labeling is used in drug packaging.
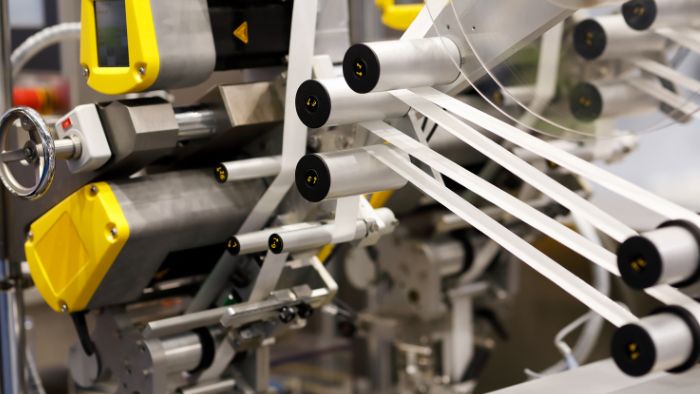
Adjusting and optimizing label peel distance with peel testing
Optimizing label peel distance is important for smooth labeling. Adjustments might be needed based on the product and labeling machine. Here are some ways to optimize label peel distance:
Testing and calibration
Regularly test and calibrate the machine. Run test labels to find the best peel distance. Use peel fixtures for more accurate tests.
Material selection
Choose the right label material and adhesive. Work with suppliers to pick materials that fit the machine well. This helps reduce the need for frequent adjustments.
Machine settings
Modern labeling machines have adjustable settings for peel distance. Operators need to learn how to use these settings for different labels and products.
Environmental considerations
Temperature and humidity can change adhesive properties. Adjust peel distance based on these conditions for consistent performance.
Regular maintenance
Keep the machine in good shape with regular maintenance. Clean and replace parts to avoid problems with peel distance settings.
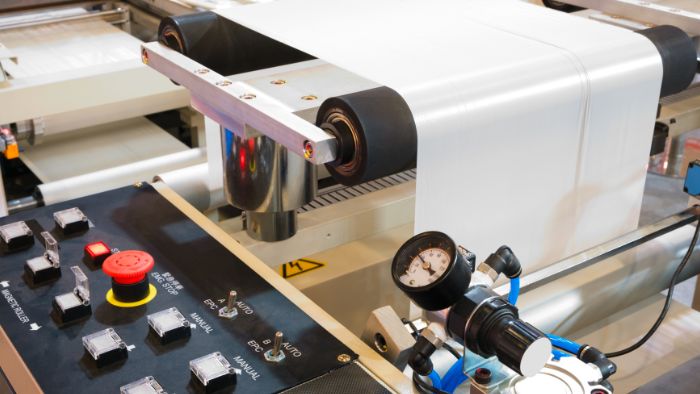
Challenges and solutions to label peel distance with peel fixtures
Achieving the right label peel distance can be hard. Common problems include:
Label tearing
If the peel distance is too short, the label might tear. Increase the peel distance or change the peel angle to fix it.
Misalignment
Wrong peel distance can make labels crooked. Adjust the peel distance and check the machine settings to avoid this.
Bubbling
If the peel distance is too long, air bubbles might form. Lower the peel distance and slow down the labeling machine.
Incomplete adhesion
Labels might not stick if the peel distance is off. Make sure the peel distance lets the label stick long enough.
Conclusion
Label peel distance is very important for labeling machines. It helps with the label’s quality and keeps the production process smooth.
By learning what affects peel distance, manufacturers can make better labels. This reduces waste and makes sure products are better. As labeling machines get better, managing label peel distance will stay important.