A differential speed separation mechanism is an advanced piece of equipment designed to separate different materials based on their varying sedimentation speeds in a centrifugal field. Differential speed separation mechanisms, such as decanter centrifuges, are instrumental in numerous industries, where precise and efficient separation of components is crucial for production quality and process efficiency.
This guide explores the principles, components, applications, and maintenance of differential speed separation mechanisms, with a specific focus on their role in labeling machines.
Understanding differential centrifugation speed separation mechanism
A differential speed separation mechanism operates on the fundamental principle of centrifugal force. When a mixture is subjected to a high-speed rotation, the components with different densities or particle sizes experience varying centrifugal forces due to different rotational speeds of the bowl and scroll, leading to their separation. This process is particularly effective for solid-liquid, liquid-liquid, and gas-solid separations.
Key components
- Centrifugal drum: The core component where the separation occurs. It provides the necessary centrifugal force to differentiate the materials based on their sedimentation speeds.
- Drive system: Comprising motors and gearboxes, the drive system supplies the rotational force required for the separation process. The speed and stability of this system are critical for effective separation.
- Control system: An automated system that monitors and regulates the separation process. It ensures consistency, precision, and safety during operation.
- Feeding and discharging system: These systems manage the continuous input of raw materials and the output of separated products. Efficient handling of materials is essential to maintain the separation process’s efficiency and throughput.
- Decanter bowl: The decanter bowl works in conjunction with the scroll to achieve effective solid-liquid separation. It plays a critical role by influencing the differential speed and residence time, which are crucial for the separation process and overall efficiency.
- Screw conveyor: The screw conveyor operates at a different speed than the bowl to efficiently transport the compacted solids out of the liquid phase. This continuous removal of solid particles enhances the effectiveness of the centrifuge’s operation.
Applications of decanter centrifuges differential speed separation mechanism
- Chemical industry: In the chemical industry, decanter centrifuges are employed to purify chemicals, separate reaction by-products, and refine raw materials. The ability to handle different phases of substances makes these mechanisms indispensable for chemical processing.
- Pharmaceutical industry: The pharmaceutical sector relies heavily on differential speed separation mechanisms for the extraction and purification of active pharmaceutical ingredients (APIs). These mechanisms effectively separate finely distributed solid particles from suspensions, ensuring that the final product meets stringent purity and quality standards.
- Food industry: In the food industry, these mechanisms are used to clarify juices, separate cream from milk, and remove impurities from various food products. The efficiency and accuracy of differential speed separation help maintain the quality and safety of food products.
- Environmental protection: Mechanical separation technology plays a crucial role in wastewater treatment and waste management. They efficiently separate solids from liquids, helping to reduce environmental pollution and facilitate the recycling of valuable resources.
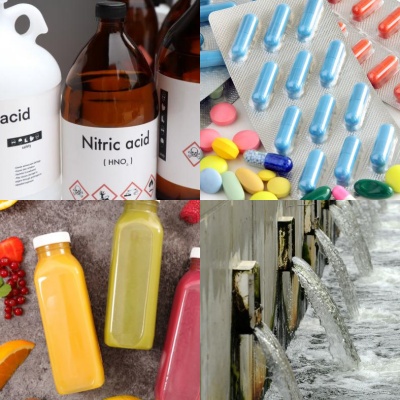
Application in labeling machines
In labeling processes, it is often necessary to handle different batches or types of products efficiently by operating at a slightly different speed. Differential speed separation mechanisms can significantly enhance the performance and accuracy of labeling machines.
Advantages and benefits
- Increased efficiency: By quickly separating different batches of products, differential speed separation mechanisms reduce downtime and increase overall production efficiency.
- High precision: These mechanisms ensure the accurate separation of solid particles, which directly translates to more precise labeling. This is particularly important in industries where labeling accuracy is critical, such as pharmaceuticals and food.
- Operational stability: The automated control systems of differential speed separation mechanisms ensure consistent and stable operation, minimizing the risk of errors and improving the reliability of labeling processes.
Practical examples
- Pharmaceutical labeling: In pharmaceutical production lines, differential speed separation mechanisms can segregate different sizes and types of pill bottles, ensuring each batch is labeled accurately and efficiently. Solid bowl decanter centrifuges play a crucial role in this process by effectively separating different sizes and types of pill bottles. Viallabeller’s pharmaceutical labeling machines utilize this setup and the machines in our pill bottle labeling solution and vial labeling solution have been well received by our customers.
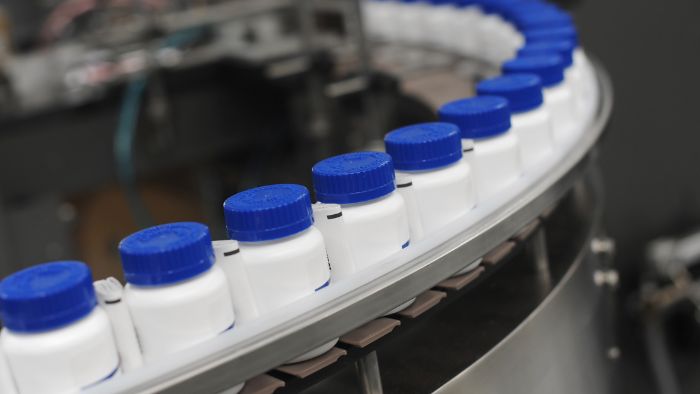
- Food packaging: In food packaging, these mechanisms can separate products by type or flavor, ensuring that labeling is specific to each product variant, thereby preventing mix-ups and maintaining product integrity.
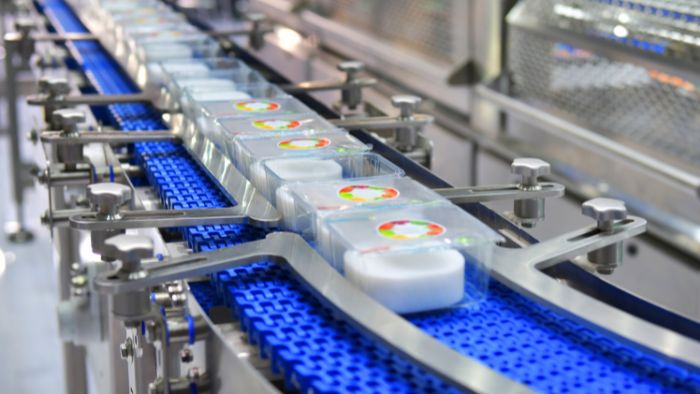
Operational considerations for rotational speed
- Regular maintenance: To ensure optimal performance, differential speed separation mechanisms require regular maintenance. This includes cleaning, inspecting worn parts, and ensuring all components function correctly. Solid shell scroll centrifuges, known for their efficiency in separating solid/liquid mixes with a high solids content, also need regular maintenance to operate continuously and effectively.
- Parameter settings: Adjusting the separation parameters according to the specific characteristics of the products being handled is essential for achieving the best results.
Difference between differential speed separation mechanism and other separation mechanisms
The differential speed separation mechanism distinguishes itself from traditional decanter centrifuges through its use of varying conveyor speeds to achieve bottle separation. Unlike decanter centrifuges that rely on differential speeds and scroll speeds to separate solid and liquid phases, the differential speed mechanism adjusts the speed of the conveyor belts to create a controlled gap between bottles. This approach minimizes mechanical wear and tear, reduces maintenance costs, and enhances reliability. Furthermore, the differential speed separation mechanism offers greater flexibility and precision, as it can easily accommodate different bottle sizes and shapes by adjusting the speed settings. This results in a smoother, more efficient separation process, leading to improved accuracy in subsequent labeling operations.
Maintenance and care
- Daily maintenance: Routine cleaning and inspection of the equipment are necessary to prevent contamination and ensure smooth operation. Checking for signs of wear and tear helps in the timely replacement of parts. Additionally, it is crucial to check and maintain optimal rotational speeds for effective separation.
- Scheduled servicing: Periodic servicing by trained professionals ensures that the differential speed separation mechanism operates at peak efficiency. This includes calibration, lubrication, and replacing worn-out components.
- Troubleshooting: Identifying and addressing potential issues promptly can prevent major breakdowns. Common problems include imbalances in the centrifugal drum, drive system malfunctions, and control system errors.
Future trends
- Smart automation: The integration of smart technologies and IoT in differential speed separation mechanisms is a significant trend. This allows for real-time monitoring, predictive maintenance, and enhanced automation, leading to improved efficiency and reduced operational costs. Additionally, advancements in mechanical separation technology are driving improvements in efficiency and automation, particularly in the operation of decanter centrifuges for various industries.
- Energy efficiency: Developing more energy-efficient differential speed separation mechanisms is a priority. This involves optimizing the design and materials used, as well as improving the drive and control systems to reduce energy consumption.
- Environmental considerations: There is a growing focus on making differential speed separation mechanisms more environmentally friendly. This includes using sustainable materials, reducing waste, and improving the recyclability of the separated materials.
Conclusion
In conclusion, the differential speed separation mechanism is a versatile and essential technology in various industries, effectively separating solid particles from liquids through strong centrifugal forces. This technology is crucial in fields ranging from pharmaceuticals to food processing and environmental protection, improving production efficiency and accuracy.
By understanding its principles, components, and maintenance needs, businesses can leverage this technology to enhance their operations and achieve higher standards of quality and productivity. As advancements continue, the differential speed separation mechanism will undoubtedly evolve, offering even greater benefits and sustainability in the future.