Understanding how to remove air bubbles and wrinkles during the labeling process is crucial for maintaining product quality and aesthetics. This guide provides detailed methods and techniques to apply labels flawlessly on various products, utilizing modern machinery and proven practices.
Addressing label problems such as air bubbles and wrinkles is essential. Effective communication and collaboration between businesses and label printing companies can help identify potential issues and troubleshoot defects, ensuring high-quality label application.
Optimizing roller machines
- Speed adjustment: The labeling machine’s speed needs to be carefully adjusted based on the container and label properties. When applying labels, high speeds with thin labels or uneven containers can cause air pockets to form as the label struggles to conform to the surface. Matching speed to the material allows for proper adhesion without air entrapment.
- Pressure balancing: Uneven pressure from the rollers can lead to bubbles and incomplete adhesion. Rollers apply pressure across the entire label surface, activating the adhesive and creating a strong bond with the container. Even pressure distribution guarantees a smooth, bubble-free application.
- Label size: Choosing the correct label size is crucial to prevent air pockets and ensure proper adhesion. Larger labels may not adhere properly due to the shape and imperfections of the surface. Adhering to specified label sizes minimizes issues such as wrinkling and bubbling during application.
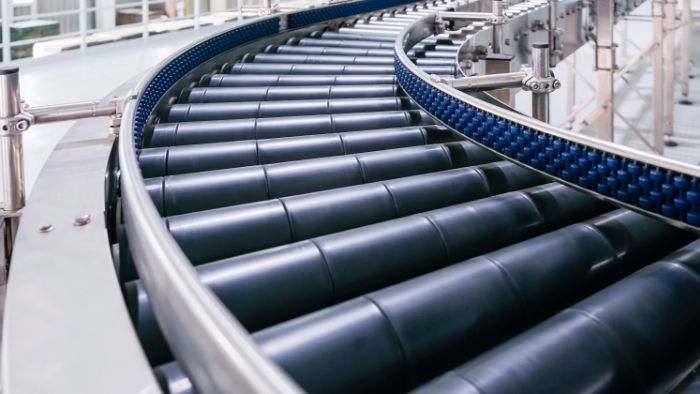
The machines in our wrap-around labeling solution are equipped with this device, which is suitable for labeling all cylindrical products and reduces the rate of product label breakage ……
Implementing a squeegee system
A squeegee system acts like a wiper, smoothing out wrinkles and eliminating trapped air during label application. The choice of material is crucial:
- Squeegee material: Rubber offers a gentle touch for delicate labels, conforming to their texture without damage. Conversely, sturdier labels might require a firmer material like metal for effective smoothing. Proper surface preparation is essential to ensure effective adhesion, making sure the surface is dry and free from contaminants like silicon, oil, dust, and oxidized materials.
- Angle adjustment: The angle at which the squeegee contacts the label significantly impacts the application. A properly adjusted angle allows the squeegee to effectively smooth the label and push out trapped air without causing wrinkles or tearing. In environments affected by moisture, using a wet-applied adhesive can mitigate peeling issues, especially when containers are wet or have condensation.
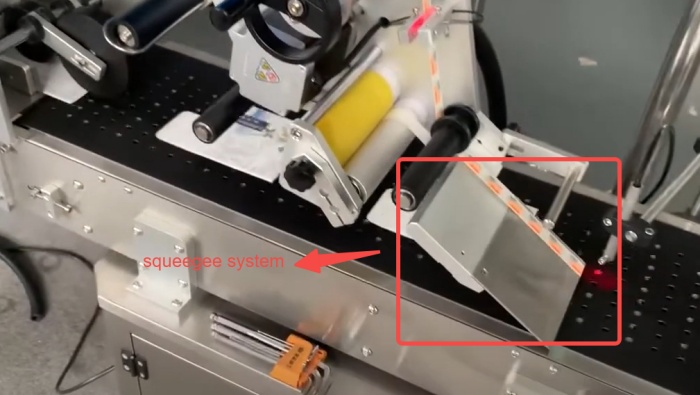
Efficiency of roll press systems
Roll press systems rely on material selection and pressure settings to achieve flawless labeling.
- Roller material: Silicone or rubber rollers excel due to their adaptability. Their flexible nature conforms to various label textures, distributing pressure evenly to prevent damage, especially for delicate labels. Selecting the appropriate label stock for various environmental conditions, such as UV exposure, moisture, and temperature fluctuations, is also essential to ensure the longevity and durability of the labels.
- Pressure settings: Finding the optimal pressure is crucial. Excessive pressure can cause wrinkles on the label, while insufficient pressure leads to incomplete adhesion. Adjusting the pressure based on label and container characteristics ensures a smooth, well-adhered label application. The practicality of large labels should also be considered, ensuring they are suitable for specific surfaces like glass bottles by adhering to manufacturer recommendations for size ratios.
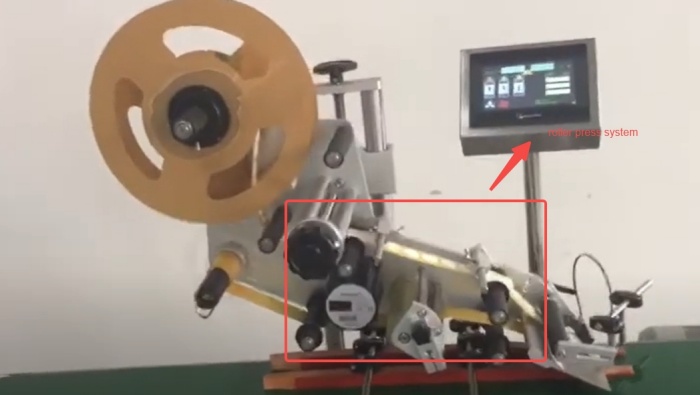
Optimizing vacuum adsorption systems to eliminate air bubbles
Vacuum systems ensure labels are flat and positioned perfectly before application. Here’s how it works:
- Adjusting suction: Suction strength needs to match the size and texture of the label. Larger or textured labels require stronger suction to overcome their weight and surface irregularities, keeping them flat and preventing curling. It is also important to obtain specifications from the label printer to ensure proper alignment.
- System maintenance: Regular checks and cleaning are crucial. Over time, dust or debris buildup can reduce suction power, hindering the system’s ability to hold the label flat. This can lead to air bubbles during application if not addressed. Additionally, requesting a spec sheet from manufacturers can prevent common labeling issues by providing precise measurements and information about the container’s shape and surface.
Precision with air blow systems
- Direction of airflow: Set the airflow direction to assist the label in laying flat against the container rather than introducing more air under the label. Air blow systems are flexible and can be configured to apply either single labels or both front and back labels, ensuring accurate and effective labeling on different container types.
- Control of air intensity: Manage the intensity of the air to be strong enough to help the label conform but not so strong as to create ripples or dislodge the label. Choosing the right label for products is crucial to ensure a bubble-free application, whether using hand or machine labeling methods.
Selecting label materials and adhesives for the labeling process
- Adaptability of materials: Choose label materials that are suited to the application, considering flexibility and thickness to reduce the likelihood of wrinkles and bubbles. Proper communication and understanding of the label application environment can help address common issues, ensuring that product labels adhere correctly and present an appealing image to potential customers.
- Type of adhesive: Use high-quality adhesives to enhance initial tackiness and reduce the chances of air being trapped under the label during application. If labels do not adhere correctly, using a hair dryer to apply gentle heat can soften the adhesive, making it easier to lift and adjust the label for a smoother application without ruining the adhesive quality.
Training and skills for operators
- Professional training: Educate operators on the principles and adjustments of different labeling equipment, including the practical aspects of applying labels to various container shapes and sizes.
- Sharing practical experience: Encourage seasoned operators to share tips and best practices to enhance the skill set of the entire team.
Maintenance and routine inspections
- Regular equipment maintenance: Keep all labeling-related machinery in good working condition with scheduled maintenance and checks. Addressing ‘label problems’ that arise during the labeling process, such as air bubbles and wrinkles, is crucial to ensure high-quality application.
- Troubleshooting and repairs: Promptly diagnose and repair any issues to prevent them from affecting the quality of labeling.
Conclusion
The importance of knowing how to apply labels and remove air bubbles and wrinkles in the labeling process cannot be overstated. Addressing label problems is crucial to ensure flawless label application.
By applying a systematic approach and comprehensive measures, businesses can ensure their labels are applied flawlessly, enhancing product appearance and consumer confidence. This guide serves as a fundamental resource for industry professionals aiming to perfect their labeling techniques and output.