It is undeniable that what is a PLC forms the cornerstone of modern industrial automation. A PLC often utilizes a graphical programming language, such as Ladder Logic or Function Block Diagram (FBD), to illustrate control system algorithms. But how exactly does this technology function?
In this article, we delve deep into the essentials of PLCs, offering a clear explanation of their role and mechanisms within the broader context of industrial processes.
What is a Programmable Logic Controller
A programmable logic controller (PLC) is a specialized computing device designed primarily for use in industrial automation and manufacturing environments. The PLC’s CPU interprets and executes program instructions, known as a PLC program, which is created and uploaded using a computer or device, thereby controlling various inputs and outputs connected to the PLC.
This technology enables precise management of machinery and assembly lines, ensuring operational efficiency and reliability in tasks that require high precision and repetitive actions.
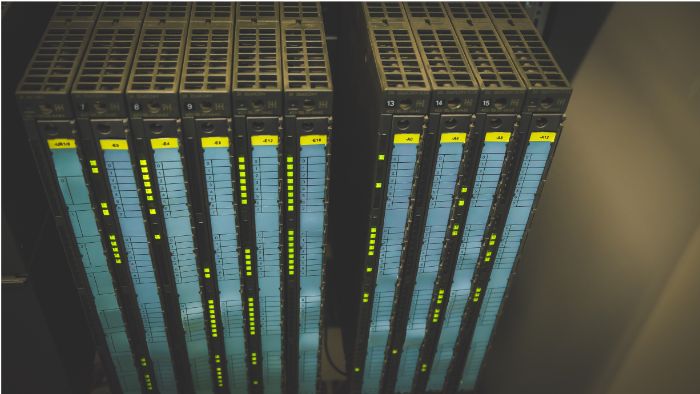
The history of the PLC
Engineer Richard E. “Dick” Morley is often referred to as the father of the PLC. In 1968, he developed the first semiconductor-based solution he called the “Modicon” (MOdular Digital Controller). It was designed to replace hardwired relay systems which had a tangle of wires and were consequently difficult to update and maintain. Traditional control mechanisms, known as relay logic systems, relied on hard-wired circuits for logic operations and were complex and difficult to maintain.
With their introduction, PLCs dramatically reduced the time, cost, and effort needed to update and modify production processes. This innovation not only simplified the physical infrastructure of control systems by eliminating extensive wiring but also introduced a higher level of flexibility in system design.
As a result, industrial automation became more streamlined and efficient, facilitating improved communication between devices and allowing for more complex and adaptable operations.
Advantages of digital control with PLCs
In stark contrast to electromechanical controllers, PLC programming is entirely digital, which means a PLC is capable of handling much more complex control tasks. One of the most commonly used programming languages for PLCs is ladder logic, which facilitates control functions in a graphical format that represents electrical circuits. If adjustments or enhancements are needed, the existing program can simply be modified or completely rewritten.
Furthermore, once a program is developed, it can be duplicated, utilized repeatedly, and enhanced with comprehensive comments and thorough documentation. This aspect greatly simplifies the process of modifying and updating programs at any subsequent point, making PLCs an incredibly versatile tool in industrial automation.
This digital approach eliminates the need for manual rewiring and reduces the potential for errors, significantly streamlining the troubleshooting and maintenance processes.
Components of a PLC
A PLC is comprised of several key components that enable its functionality:
- CPU (Central processing unit): Acts as the brain of the PLC, processing all data from the inputs to execute the control program and sending commands to the outputs.
- Inputs: These are interfaces like sensors that provide real-time data to the PLC regarding operational conditions.
- Input and output devices: These devices are crucial for monitoring and controlling industrial processes. They allow the PLC to be customized for scalability and adaptability in various applications.
- Program: The set of instructions written by the user that dictates how the PLC should operate based on the inputs received.
- Outputs: Components like actuators or relays that enact the decisions made by the PLC’s CPU.
The Functionality of PLC
The operation of a programmable logic controller (PLC) involves several key steps that ensure effective control and automation:
- Detection of input device states: The PLC constantly monitors the state of various input devices connected to it.
- Discrete inputs: These inputs represent binary states, such as on/off, 1/0, open/closed. Examples of discrete inputs include a push button switch, which can be either on or off, or a valve, which may be open or closed.
- Analog inputs: Contrary to discrete, analog inputs signify data across a continuum of values. They are essential for measuring variables such as temperature, pressure, carbon dioxide levels, or weight. For instance, a temperature sensor may record a continuous range of temperature from freezing to boiling points.
- Execution of program instructions: Based on the data received from these inputs, the PLC processes and executes predefined program instructions. This programming determines how the PLC responds to different input conditions, allowing for dynamic and responsive automation. A function block diagram (FBD) is often used to illustrate signal and data flow through reusable function blocks, modeling the interconnections between control system algorithms and logic.
- Operation of output devices: Following the execution of its program, the PLC sends signals to output devices to perform actions based on the inputs and the program’s logic.
- Examples of output devices include alarms, which may sound under specific conditions; indicator lights, which provide visual feedback; valves, which control fluid flow; and visual displays, which show system statuses or alerts.
Applications
Applications of PLCs in daily life
Programmable Logic Controllers (PLCs) are deeply integrated into various aspects of everyday life, often operating behind the scenes to enhance efficiency and safety without our direct knowledge.
- Street lighting: One of the more visible applications of PLCs is in the management of street lighting. Controlling these systems helps cities save significant energy and reduce costs, as street lighting can consume a substantial portion of a city’s utility budget, sometimes accounting for 35-45% of the total expenditure.
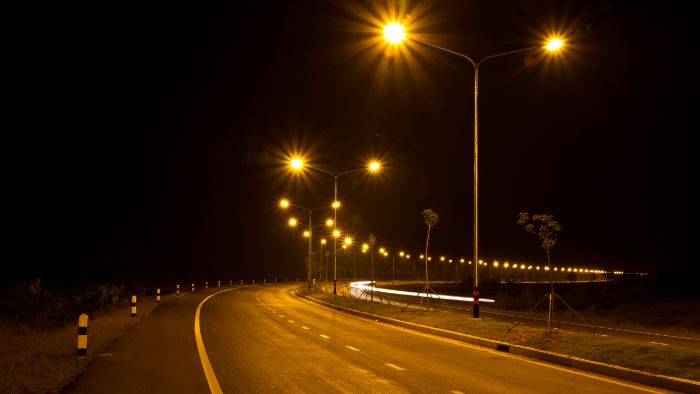
With smart PLC-based systems, street lighting expenses can be cut by up to 70%. These systems use real-time data such as time of day, light sensor feedback, and detection of pedestrians or vehicles to optimize when lights are turned on or off.
Additional everyday applications:
- Traffic light circuits: PLCs manage the sequence and timing of traffic lights, improving flow and reducing congestion.
- Digital signage: These signs change content dynamically, using PLCs for timely updates and adjustments.
- Automotive systems: In vehicles, PLCs are used for controlling electric windshield wipers and fuel injection pumps, adapting their operation based on driving conditions.
- Home automation: This includes automatically controlled shutters, heating control systems, and gate systems, which adjust based on environmental inputs and homeowner preferences.
- Vertical transportation: Elevators and escalators use PLCs for precise control of movement, ensuring safety and efficiency in their operation.
The role of PLCs in industrial processes
In the realm of industrial manufacturing, the advent of programmable logic controllers (PLCs) has revolutionized the way processes are monitored and controlled. These electronic, logic-based systems are indispensable for automating complex manufacturing tasks, significantly reducing time, costs, and labor.
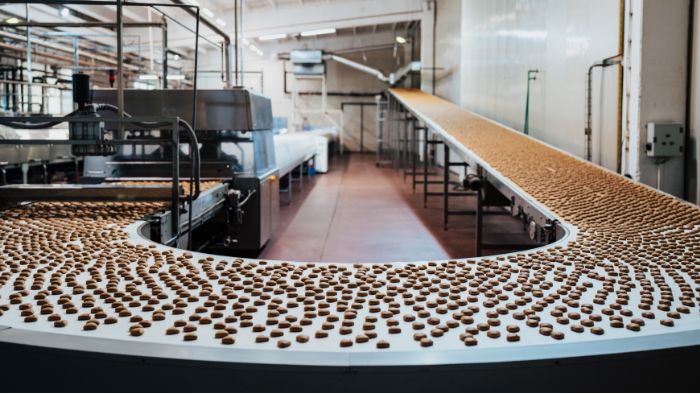
Example in food industry operations:
A practical application of PLCs is in the food production sector. For instance, during the manufacturing of potato chips, a PLC can be integral in ensuring quality control. Here’s how the system typically works:
- Input detection: Light sensors installed along the conveyor belt serve as the input devices for the PLC. These sensors detect the color of each potato chip passing by on the conveyor.
- Logical processing: Based on the input from the light sensors, the PLC’s program logic determines the exact timing and activation of specific blowers. The logic is programmed to identify darker, likely burnt chips.
- Output activation: Once a burnt chip is detected, the PLC activates targeted blowers at precise locations along the belt. These blowers are used to remove the burnt chips from the production line, thus maintaining the quality of the batch.
Further industrial applications:
- Robotic operations: In automotive manufacturing, PLCs control robots that perform tasks such as welding and parts assembly, enhancing precision and speed.
- Assembly lines: PLCs synchronize the operation of conveyor belts and machinery to optimize the assembly process, such as in electronics manufacturing. Our company specializes in the development of labeling machines and has a number of labeling solutions, such as syringe labeling solutions and tamper-evident labeling solutions, which use PLCs to achieve increased assembly efficiency.
- Machine functions: In textile manufacturing, PLCs regulate the operation of looms and other machinery, adjusting parameters for different fabric types and designs.
Integrating PLCs within SCADA systems
Programmable Logic Controllers (PLCs) are commonly integrated as crucial components of Supervisory Control and Data Acquisition (SCADA) systems. These decentralized systems are designed to monitor, visualize, and control operations throughout industrial environments, with PLCs and Remote Terminal Units (RTU) handling the majority of these control tasks.
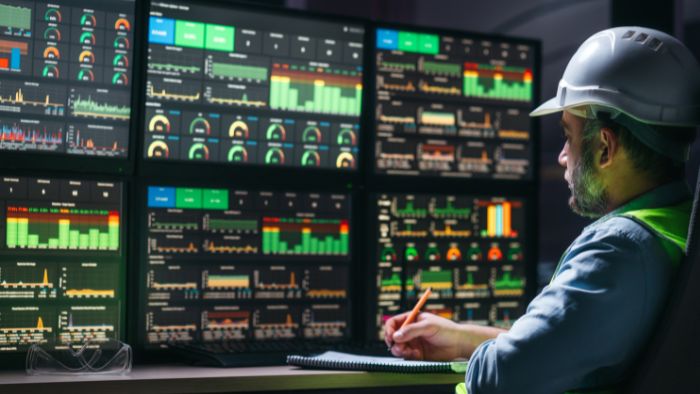
Data collection and interaction process:
- Data collection: The process begins with PLCs gathering data from various machines on the production floor. These controllers serve as the primary interface for real-time data acquisition, collecting inputs on operational parameters and machine status.
- Data visualization and interaction: After collection, this data is relayed to Human Machine Interfaces (HMIs), which visualize the information for operators. HMIs play a vital role in making complex data comprehensible, enabling operators to see trends and receive alerts.
- SCADA software interaction: Operators interact with the SCADA system through software platforms such as Ignition. This software allows for sophisticated data analysis, system management, and decision-making support by providing tools to manipulate and delve deeper into the data collected by the PLCs.
Extended system capabilities:
- Remote monitoring and control: Beyond local control, SCADA systems enable remote monitoring and equipment operation, allowing decisions to be made from centralized control rooms that can manage multiple sites.
- System scalability and integration: PLCs within SCADA systems can easily be scaled to accommodate expanding operations or to integrate new technologies and equipment, making them adaptable to changing industrial demands.
- Enhanced operational efficiency: By automating the data collection and response processes, PLCs reduce the likelihood of human error, increase the speed of response to potential issues, and optimize production processes, thereby enhancing overall operational efficiency.
Differences between a PLC and an industrial computer
Industrial computers are often considered the core of Industry 4.0, functioning similarly to PLCs in terms of receiving inputs, producing outputs, and controlling automation processes. However, there are distinct differences between how automation is controlled by a PLC versus an industrial computer.
One key difference is the variety of programming languages used for programming PLCs, as defined by the International Electrotechnical Commission (IEC) 61131.
Interfaces and connections
While a PLC offers a robust selection of I/O options, its connectivity is generally more restricted compared to an industrial PC. Industrial PCs can interface with a broader array of external devices including displays, drivers, printers, network interface cards, and peripherals from various manufacturers. The flexibility of various I/O options and card slots allows an industrial PC to be highly customizable and expandable according to specific needs.
For instance, an industrial PC can accommodate enhancements like wireless or cellular cards, Human Machine Interfaces (HMI), or vision systems, broadening its application scope significantly. Nonetheless, to fully replace a PLC, an industrial PC must be equipped with the appropriate software stack, ensuring it can meet the specific requirements of industrial automation control.
Performance and storage
Industrial PCs boast superior processor performance and enhanced storage capabilities compared to PLCs. These features provide significant advantages, particularly in handling complex data analysis, extensive data logging, and integrating advanced technologies such as artificial intelligence and machine learning.
Additionally, the programming flexibility offered by industrial PCs enables them to manage complicated scenarios more effectively. Another benefit of industrial PCs is their ability to consolidate workloads, which is especially valuable in environments where space is at a premium.
By reducing the hardware footprint, industrial PCs can optimize the use of physical space while maintaining high-performance levels. This makes them ideal for sophisticated industrial applications where efficiency and space utilization are critical.
Security considerations
PLCs operate with a very simple, dedicated operating system developed specifically for the control tasks at hand. This focused and minimalistic software approach tends to minimize the security vulnerabilities often found in more complex consumer operating systems.
On the other hand, an industrial PC requires a more versatile operating system to run a variety of applications, potentially raising questions about its susceptibility to cyberattacks.
However, modern industrial PCs are designed with robust security features to mitigate these risks. Moreover, the widespread use of PCs ensures that security vulnerabilities are identified and addressed quickly through regular updates.
In contrast, PLCs are updated less frequently and rely on older technology, which can lead to a less secure environment over time. This difference highlights the need for proactive security measures, particularly in critical industrial applications where the impact of a security breach could be severe.
Durability
When comparing the durability of PLCs to industrial computers, it’s important to note that both are designed to withstand the harsh conditions typically found in industrial settings.
Unlike conventional PCs, both PLCs and industrial PCs are built to endure extreme temperatures, dust, moisture, and vibrations, ensuring reliable performance even in challenging environments.
This robust construction is critical as it prevents operational disruptions and maintains continuous industrial processes.
Future outlook
With the advancement of technology, the application of PLC in the fields of automation and intelligent manufacturing will become more extensive and in-depth. Future PLCs may integrate more advanced data processing capabilities and artificial intelligence algorithms, allowing them to handle complex control tasks and data analysis more intelligently.
In addition, with the development of Internet of Things (IoT) technology, PLCs may be more closely integrated with cloud computing and big data technologies to achieve more efficient remote monitoring and management, greatly improving production efficiency and safety.
At the same time, the design of PLCs may pay more attention to energy efficiency and environmental protection, in line with the requirements of global sustainable development.
Conclusion
In sum, the significance of what is a PLC in the realm of industrial automation cannot be overstated. These programmable logic controllers have reshaped how industries operate by providing robust, reliable, and efficient control over complex processes.
By allowing for extensive customization, quick programming updates, and seamless integration with other technological advancements, PLCs continue to be a cornerstone in the development of automated systems that enhance productivity and reduce operational risks.
As a pharmaceutical labeling equipment automation company, PLC helps us to improve the assembly efficiency of our machines in the following ways: helping our labeling machines to adapt to different types and sizes of labels, achieving accurate label attachment, and detecting and recording the operating status and fault information of the labeling machines.
In addition to the tamper-evident labeling machine and syringe labeling machine, we have other machine solutions that utilize PLCs, as follows:
Auto-injector labeling solution
Pharma carton labeling solution
References and citations
- Mark Walker, The PLC: A Logical Development, Measurement and Control, Volume 43, Issue 9, November 1, 2010, doi: https://doi.org/10.1177/002029401004300904
- Ephrem Ryan Alphonsus, Mohammad Omar Abdullah, A review on the applications of programmable logic controllers (PLCs), Renewable and Sustainable Energy Reviews, Volume 60, July 2016, Pages 1185-1205, doi:https://doi.org/10.1016/j.rser.2016.01.025
- Jeff Payne, Future of PLC, Control Engineering(Vol. 61, Issue 9), Sept. 2014.