A spring buffer pressing mechanism is an integral component in various mechanical systems, designed to mitigate shock and manage kinetic energy through compression and decompression of springs.
This mechanism plays a crucial role in enhancing machinery lifespan and efficiency by absorbing sudden forces or impacts that could otherwise cause damage. This article explores the fundamental aspects, operation, design principles, and applications of spring buffer pressing mechanisms. The present invention relates to innovations in slide rail technology for cabinets, including self-closing buffers and automatic rebound mechanisms.
Overview and functionality
Spring buffer pressing mechanisms utilize the physical properties of springs to absorb energy. When external force is applied, the spring compresses, storing potential energy that is gradually released as the spring returns to its original position. This action helps in damping vibrations and reducing the impact of shock forces on mechanical components.
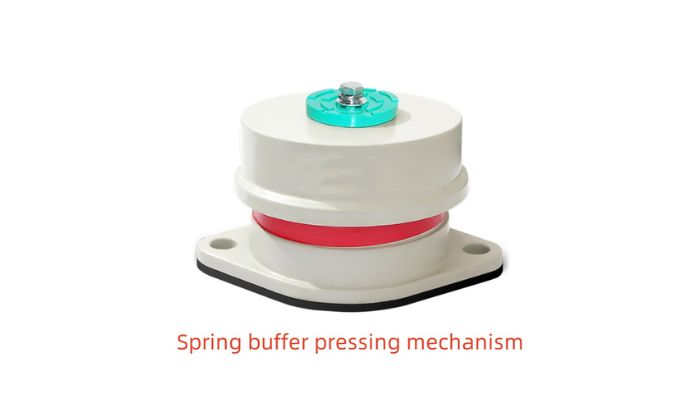
Key components
- Springs: Typically made from steel or other durable materials, these are the core elements where energy is stored and dissipated.
- Buffers: These are often incorporated to enhance the energy absorption capacity and provide additional stability.
- Pressing plates: These components distribute the force evenly across the spring, ensuring effective operation.
The mechanism comprises several key components that work together to improve performance, safety, and user convenience.
Design considerations
Designing a spring buffer pressing mechanism involves several critical considerations:
- Material selection: The choice of material affects the durability and performance of the spring. High-carbon steel is commonly used for its resilience and fatigue resistance.
- Spring configuration: The shape and size of the spring (e.g., coil, leaf) are determined based on the specific application requirements.
- Load capacity: The mechanism must be capable of handling the maximum expected load without failure.
The preferred embodiment of the spring buffer pressing mechanism includes detailed illustrations and explanations of the best design approach to achieve optimal functionality.
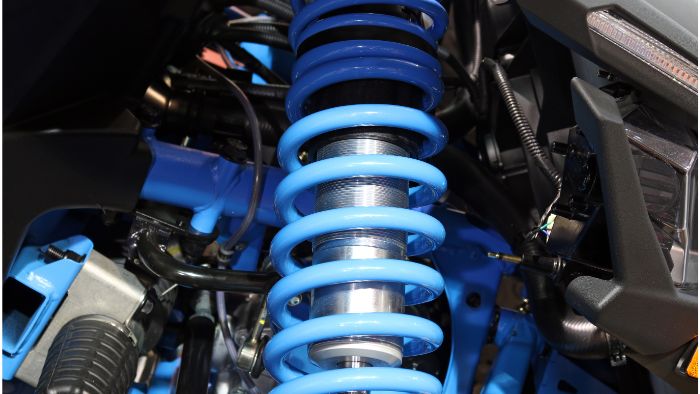
Applications in industry
Spring buffer pressing mechanisms are found in various applications:
- Automotive: In shock absorbers to improve ride quality and vehicle handling. Additionally, slide rail mechanisms with buffer functions are used in automotive interiors to enhance the safety and efficiency of drawer operations.
- Manufacturing equipment: To protect machinery from damage due to mechanical overload.
- Consumer electronics: In devices where cushioning is necessary to protect sensitive components.
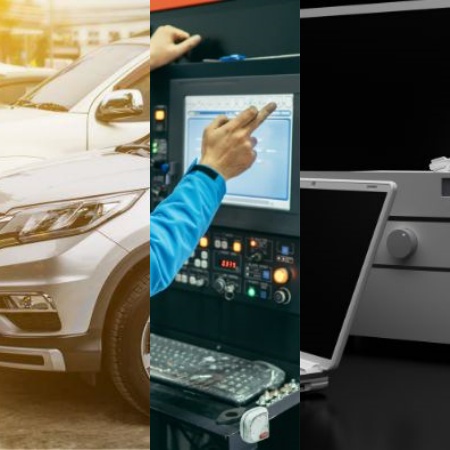
Advantages of using spring buffer pressing mechanisms
- Increased equipment lifespan: By reducing mechanical stress, these mechanisms extend the operational life of machinery.
- Enhanced safety: They play a critical role in preventing accidents and equipment failure by managing unexpected loads through fixed connections of components like support boards and gripper shoes.
- Cost efficiency: Reducing maintenance and repair costs through effective shock absorption.
Challenges and innovations
Despite their benefits, designing and implementing spring buffer pressing mechanisms pose challenges such as the position of components within the system:
- Material fatigue: Over time, repeated compressing and decompressing can lead to wear and tear.
- Environmental factors: Variables like temperature and humidity can affect performance, necessitating robust design adaptations.
Conclusion
In summary, the spring buffer pressing mechanism is a vital technology in modern engineering, providing essential protection against physical shocks and vibrations across numerous industries.
As technology progresses, the development of more advanced materials and designs will further enhance the capabilities of these mechanisms, making them even more integral to industrial and consumer applications. Understanding the intricacies of these systems is crucial for engineers and designers aiming to optimize the safety and durability of mechanical systems. The present invention focuses on innovative self-closing buffers and automatic rebound mechanisms, enhancing user convenience and safety.
Our labeling machines are also equipped with this mechanism. As a classic brand of pharmaceutical labeling machines, Viallabeller is, of course, responsible for the durability of the machine. We also have a range of pharmaceutical labeling solutions: